Differenze tra le versioni di "Ebanite/en"
(Creata pagina con "left|thumb|Example of discoloration of a [[Swan in ebonite]]") |
|||
(15 versioni intermedie di 2 utenti non mostrate) | |||
Riga 1: | Riga 1: | ||
− | [[ | + | [[File:Montblanc-InkBottle-Closed.jpg|thumb|An ebonite [[Montblanc]] travel inkwell]] |
The <includeonly>[[Ebonite]]</includeonly><noinclude>Ebonite</noinclude> (often called ''hard rubber'' or also ''vulcanite'' in some old advertisements) is a <includeonly>material</includeonly><noinclude>[[materials|material]]</noinclude> invented<ref>see the [http://it.wikipedia.org/wiki/Ebanite italian] and [http://en.wikipedia.org/wiki/Ebonite english] entries of Wikipedia, which, however, present some discrepancies, in particular on the attribution of the invention to O. Meyer and T. Hancock for the first and Charles Goodyear for the second.</ref> in 1843 and produced by a rubber vulcanization process in which the natural rubber is mixed with a variable percentage (from 20 to 50%) of sulfur, and hardened by keeping it at high temperature for a prolonged time (a few hours around 150°C). Hard rubber is generally produced in sheets, bars or slabs, which must be subsequently processed; in fact, it is not possible to make it with a mould. | The <includeonly>[[Ebonite]]</includeonly><noinclude>Ebonite</noinclude> (often called ''hard rubber'' or also ''vulcanite'' in some old advertisements) is a <includeonly>material</includeonly><noinclude>[[materials|material]]</noinclude> invented<ref>see the [http://it.wikipedia.org/wiki/Ebanite italian] and [http://en.wikipedia.org/wiki/Ebonite english] entries of Wikipedia, which, however, present some discrepancies, in particular on the attribution of the invention to O. Meyer and T. Hancock for the first and Charles Goodyear for the second.</ref> in 1843 and produced by a rubber vulcanization process in which the natural rubber is mixed with a variable percentage (from 20 to 50%) of sulfur, and hardened by keeping it at high temperature for a prolonged time (a few hours around 150°C). Hard rubber is generally produced in sheets, bars or slabs, which must be subsequently processed; in fact, it is not possible to make it with a mould. | ||
− | Ebonite is a hard and brittle material, very resistant to corrosion by acids, and softens when heated. It is an excellent electrical insulator. It is easy to process and has been used both for the construction of objects and as an electrical insulator (use that still holds today). It owes its name<ref>the | + | Ebonite is a hard and brittle material, very resistant to corrosion by acids, and softens when heated. It is an excellent electrical insulator. It is easy to process and has been used both for the construction of objects and as an electrical insulator (use that still holds today). It owes its name<ref>the ''ebonite'' one, still beeing much more commonly called ''hard rubber'' as ''ebonite'' was a trade name.</ref> because it was initially used as a substitute for ebony. Its chemical resistance characteristics have seen it used for many years as an insulator, coating for corrosion-prone parts and as a battery case for cars. |
Ebonite is the first material used for the production of fountain pens, in use since the first examples produced at the end of 1800. If even some objects considered as "precursors" of the fountain pen were made of metal, the first fountain pens were born substantially as a result of the invention of this material, which with its characteristics of ease of use, chemical inertia (and consequent resistance to corrosion), proved to be optimal for the construction of that "reservoir" of ink that was in fact the main component of the first fountain pens, and this also thanks to its characteristics of thermal insulation, which avoid the transmission of heat from the hand to the air of the reservoir, with a consequent increase in pressure and loss of ink. | Ebonite is the first material used for the production of fountain pens, in use since the first examples produced at the end of 1800. If even some objects considered as "precursors" of the fountain pen were made of metal, the first fountain pens were born substantially as a result of the invention of this material, which with its characteristics of ease of use, chemical inertia (and consequent resistance to corrosion), proved to be optimal for the construction of that "reservoir" of ink that was in fact the main component of the first fountain pens, and this also thanks to its characteristics of thermal insulation, which avoid the transmission of heat from the hand to the air of the reservoir, with a consequent increase in pressure and loss of ink. | ||
− | [[File:Swan-SelfFiller-SF2-Inscr.jpg|left|thumb|Example of discoloration of a [[Swan]] in ebonite]] | + | [[File:Swan-SelfFiller-SF2-NoClipBCHR-Inscr.jpg|left|thumb|Example of discoloration of a [[Swan]] in ebonite]] |
− | + | The material, however, suffers from high mechanical fragility, which makes the ebonite pens not very resistant to shocks and falls, in this case the chemical neutrality proves a defect as it makes it almost impossible to glue pieces of ebonite together in a resistant manner.<ref>see [http://forum.fountainpen.it/viewtopic.php?f=12&t=9228#p115300 this discussion].</ref> Furthermore, with exposure to light, humidity and heat, the sulphur present in the material tends to oxidise, and to emerge on the surface, colouring it with a sort of dark brown opaque film that removes the lustre of the original polish. This patina is an indication of the age of a pen, and even if today there are products that can reverse the process and bring the material back to its original shine, the opportunity for such an operation is questioned by those who do not consider it respectful of the state of the pen.<ref>see [http://forum.fountainpen.it/viewtopic.php?f=12&t=2134 this discussion].</ref> | |
− | + | In addition to mechanical fragility, the other fundamental defect of ebonite, at least from the point of view of fountain pen manufacturers, is the substantial impossibility of colouring. For this reason, for a long time, the two ways of enriching the aesthetic aspect of pens were chiselling, to which ebonite lends itself with relative ease, and coating with machined metal skeletons. In the first case we have what is called in jargon ''Black Chased Hard Rubber'' ([[BCHR]]), in the second case the countless variations of the [[overlay|coatings]]. | |
− | + | The natural color of ebonite is black, the only other colors that can be obtained with relative ease are orange, thanks to the use of cinnabar, or dark red (with the use of hematite).<ref>for more technical details you can refer to this [https://web.archive.org/web/20120106092952/http://www.kamakurapens.com/Archive/TheRHRPen.html article].</ref> This has given rise to several processes, from the classic [[RHR|red hard rubber]], to the various combinations of red and black ebonite ([[Mottled]], [[Rippled]], etc..) up to the production, carried out essentially by the [[Waterman]]<ref>even if some [[Tibaldi]] [[Tibaldi Flattop|models]] in coloured ebonite are known.</ref> in its obstinacy not to abandon this material, of colours such as green, blue, yellow and pink. But in the end none of these colours could compete with the brilliance offered by the new materials, and in particular by the [[celluloid]], and ebonite has been progressively abandoned as a material used for the body of the pen, remaining however used until today in the production of the [[feed]]s.<ref>even if today this happens only for the most valuable pens, since this material cannot be moulded.</ref> | |
<noinclude> | <noinclude> | ||
− | == | + | == External References == |
+ | * [https://web.archive.org/web/20120106092952/http://www.kamakurapens.com/Archive/TheRHRPen.html] Article about red ebonite | ||
+ | * [http://www.bouncing-balls.com/chemistry_tech_conservation/ageing.htm] On the degradation of vulcanised rubber | ||
+ | * [http://forum.fountainpen.it/viewtopic.php?f=12&t=2134] A forum discussion about ebonite cleaning | ||
+ | * [http://forum.fountainpen.it/viewtopic.php?f=12&t=9228#p115300] A discussion on the reconstruction of ebonite with cyanoacrylate | ||
+ | == Notes == | ||
<references/> | <references/> | ||
− | + | [[Category:Translated Pages]] | |
− | |||
− | |||
− | |||
− | |||
− | |||
</noinclude> | </noinclude> |
Versione attuale delle 15:23, 4 apr 2023
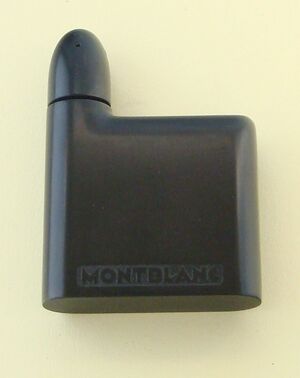
The Ebonite (often called hard rubber or also vulcanite in some old advertisements) is a material invented[1] in 1843 and produced by a rubber vulcanization process in which the natural rubber is mixed with a variable percentage (from 20 to 50%) of sulfur, and hardened by keeping it at high temperature for a prolonged time (a few hours around 150°C). Hard rubber is generally produced in sheets, bars or slabs, which must be subsequently processed; in fact, it is not possible to make it with a mould.
Ebonite is a hard and brittle material, very resistant to corrosion by acids, and softens when heated. It is an excellent electrical insulator. It is easy to process and has been used both for the construction of objects and as an electrical insulator (use that still holds today). It owes its name[2] because it was initially used as a substitute for ebony. Its chemical resistance characteristics have seen it used for many years as an insulator, coating for corrosion-prone parts and as a battery case for cars.
Ebonite is the first material used for the production of fountain pens, in use since the first examples produced at the end of 1800. If even some objects considered as "precursors" of the fountain pen were made of metal, the first fountain pens were born substantially as a result of the invention of this material, which with its characteristics of ease of use, chemical inertia (and consequent resistance to corrosion), proved to be optimal for the construction of that "reservoir" of ink that was in fact the main component of the first fountain pens, and this also thanks to its characteristics of thermal insulation, which avoid the transmission of heat from the hand to the air of the reservoir, with a consequent increase in pressure and loss of ink.
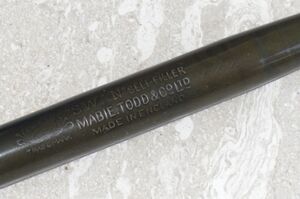
The material, however, suffers from high mechanical fragility, which makes the ebonite pens not very resistant to shocks and falls, in this case the chemical neutrality proves a defect as it makes it almost impossible to glue pieces of ebonite together in a resistant manner.[3] Furthermore, with exposure to light, humidity and heat, the sulphur present in the material tends to oxidise, and to emerge on the surface, colouring it with a sort of dark brown opaque film that removes the lustre of the original polish. This patina is an indication of the age of a pen, and even if today there are products that can reverse the process and bring the material back to its original shine, the opportunity for such an operation is questioned by those who do not consider it respectful of the state of the pen.[4]
In addition to mechanical fragility, the other fundamental defect of ebonite, at least from the point of view of fountain pen manufacturers, is the substantial impossibility of colouring. For this reason, for a long time, the two ways of enriching the aesthetic aspect of pens were chiselling, to which ebonite lends itself with relative ease, and coating with machined metal skeletons. In the first case we have what is called in jargon Black Chased Hard Rubber (BCHR), in the second case the countless variations of the coatings.
The natural color of ebonite is black, the only other colors that can be obtained with relative ease are orange, thanks to the use of cinnabar, or dark red (with the use of hematite).[5] This has given rise to several processes, from the classic red hard rubber, to the various combinations of red and black ebonite (Mottled, Rippled, etc..) up to the production, carried out essentially by the Waterman[6] in its obstinacy not to abandon this material, of colours such as green, blue, yellow and pink. But in the end none of these colours could compete with the brilliance offered by the new materials, and in particular by the celluloid, and ebonite has been progressively abandoned as a material used for the body of the pen, remaining however used until today in the production of the feeds.[7]
External References
- [1] Article about red ebonite
- [2] On the degradation of vulcanised rubber
- [3] A forum discussion about ebonite cleaning
- [4] A discussion on the reconstruction of ebonite with cyanoacrylate
Notes
- ↑ see the italian and english entries of Wikipedia, which, however, present some discrepancies, in particular on the attribution of the invention to O. Meyer and T. Hancock for the first and Charles Goodyear for the second.
- ↑ the ebonite one, still beeing much more commonly called hard rubber as ebonite was a trade name.
- ↑ see this discussion.
- ↑ see this discussion.
- ↑ for more technical details you can refer to this article.
- ↑ even if some Tibaldi models in coloured ebonite are known.
- ↑ even if today this happens only for the most valuable pens, since this material cannot be moulded.