Filling systems
The creation of new filling systems has always been, especially in the golden age of the development of the fountain pen, one of the major factors of technical innovation, and for this reason also the birth of new companies; In this field the most famous examples are the Conklin, born for the invention of the Crescent filler and the Sheaffer, which entered the market with the creation of the lever filler, but many other less known companies (such as the Onoto, the Dunn, the Moore or the Chilton) have had a similar origin.
The history of the fountain pen is in fact inextricably linked to that of the various systems that over the years have been designed to fill the ink. In particular, in the early 1900s all manufacturers competed to introduce new filling systems, often unnecessarily complicated and not very functional, which were then used to promote the superiority of their pens.
Below are the main loading systems used by the various manufacturers throughout the long history of the fountain pen from its origins to the present day. The various systems have been grouped by affinity of operation, and the various groups are presented in an approximate chronological order of introduction.
Direct filling
This first grouping includes all those filling systems that require the pen to be loaded by directly inserting the ink into the barrel. These are the most primitive loading systems, used at the beginning of the fountain pen history. In most cases they have been replaced since the beginning of the 1900s by systems that allow automatic filling.
In the systems illustrated in this section, the body of the pen also acts as a tank, and there is no mechanism to automate the loading of the ink, which is usually entered by an eyedropper; the variants proposed relate only to the different methods used to give access to the tank.
eyedropper filler
The eyedropper filler, also called drop filler, is the first filling system used in fountain pens and in reality it cannot be considered even a real filling system, since in essence there is no "system".
In this case, in fact, the pen is filled by removing the nib assembly from the barrel, which is used directly as a tank. The refill operation is carried out, once the access to the tank has been obtained, with the introduction of ink to be carried out usually with a dropper, which in the original versions was supplied by the manufacturer together with the pen. Once the refill was completed, the nib assembly had to be reassembled on the barrel in order to use the pen.
Because of its simple construction, this "system" was adopted by all manufacturers from the 19th century to the dawn of the development of the fountain pen, and remained in use until the beginning of the 20th century. The system is simple, especially in terms of technical requirements for construction, and also has the advantage of allowing a large capacity of ink, greater than any other, as determined only by the size of the pen body.
However, it has many drawbacks, the first of which is undoubtedly the inconvenience of filling operations, since to refill a pen you have to disassemble the section with the nib, usually wet with ink, and store it in a separate place where it does not stain and does not risk falling. The refill operations are very uncomfortable, it is necessary to have a dropper or similar tool, and in general the operation of the transfer of ink, having to keep always well vertical the body of the pen that acts as a reservoir, is delicate and at risk of stains and spills of ink.
A second drawback arises from the fact that with wear, especially in lower quality models, having the ink in direct contact with the body of the pen can cause leaks at the junction between the barrel and nib group once it loses the seal. Moreover, having to unscrew and screw the latter, the risk of staining the hands, especially in the presence of a body that has been full of ink until then, is always quite high. The body of the pen then had to be made only of inert material that was able to resist contact with the corrosive agents present in the inks, which at the time of its introduction was only the hard rubber.
A last drawback, often very annoying, is that since in this case the ink contained directly in the body of the pen, when it is emptied, there is a considerable sensitivity to changes in pressure and temperature of the air contained within the pen barrel, which is the greater the greater the volume available. The biggest problems were then in the case of air travel, where variations in altimetric pressure invariably caused a leakage of ink.
But with these pens to cause a leak is often sufficient only the heat of the hand that holds the pen. This is transmitted to the air contained inside the barrel, causing an expansion that alters the balance of pressure between inside and outside. This makes it relatively easy to obtain a loss of ink. Although today it is back in fashion in some models, for its retro taste, it remains, however, provided that it can really be considered as such, a primitive filling system.
safety filler
The filling system called safety filler was born as an evolution of the eyedropper filler system. To simplify the filling operations without having to disassemble and store the section with the nib unit, and to avoid ink leakage as a result of differences in pressure and temperature, in this case the nib is mounted on a mechanism that allows you to retract it inside the body of the pen. From this feature comes also the name of retractable with which we often identify the pens that use this filling system.
The system involves that, after inserting the nib into the body of the pen, the latter becomes accessible for filling, to be done with the usual eyedropper, and with the same problems (except that of storing the nib group in a safe place) as previously seen. In this case there is less volume available for the ink, as the inside of the barrel is also occupied by the mechanism, but always more than enough. To use the pen, simply reuse the mechanism in reverse to return the nib to the working position, making it come out of the body of the pen.
Once the nib has returned to the inside of the barrel, the pen can be hermetically sealed using a flat-bottomed cap equipped with suitable gaskets that allow it to be totally guaranteed against the leakage of ink, a characteristic to which the name safety is due, with which the pens equipped with this filling system are called. In this case, in fact, there is no possibility that the ink, due to pressure imbalances, can escape from the nib and deposit in the cap, since the latter simply serves as a cap for the barrel; all pressure imbalances are then immediately eliminated when the cap is opened.
This safety feature was a big step forward at a time when ink leaks were very common, and the holding of the caps, often simply locked by pressure on the pen barrel, was very problematic. From this point of view, pens safety remain superior to any modern pen. Moreover, the hermetic closure of the cap, which also includes the nib assembly, allows to reduce to practically zero the possibility of evaporation of the ink, which is very difficult to dry inside the pen, thus allowing the use of inks much thicker than the ordinary ones. For these peculiar characteristics Waterman has continued to produce a line of these pens, aimed at artists and musicians and aviators, until the early '40s.
The charm of this filling system lies in the mechanical complexity of its realization, which often shows the pinnacle of the technologies of the time: in fact, the nib group is generally moved thanks to a helical screw driven by the rotation of the bottom of the pen. In working position it will hermetically close the barrel by means of a gasket, while in rest position it will leave complete access to the inside of the pen.
With these pens it is essential to remember to open the cap always in a vertical position, and never to close it without having first retracted the nib inside the barrel, to avoid damaging the tip. Since this was a common drawback, some models (the first introduction of this innovation is attributed to Montblanc) require the presence of a special safety mechanism (usually a pin mounted in the center of the cap that beats on the nib assembly), which thus prevents it from closing if it has not been completely withdrawn inside the body of the pen.
The safety filler was born in the United States in the last decade of 1800, although it is not possible to define precisely an inventor, its massive introduction on the market is attributed to Waterman, which was the main manufacturer to adopt it on a large scale.[1] However, it has had a much greater success in Europe, where at the beginning of the century practically all the producers (and in particular the German ones, among which the Kaweco stands out, who also made some developments) made use of this system, and where it has remained in production much longer.
Although it is classified, perhaps unjustly, among the primitive loading systems, in reality the safety filler has resisted on the market much longer than other filling systems created in later periods. In particular, in Europe there are mass-produced models that use it until after the war. Because of its historical value, which sees it as substantially the first mechanical system dedicated to filling the pen, it continues to receive an undeniable interest from collectors, many of whom have a particular preference for safety pens.
non-leakable filler
A notable variant of the safety filler is the peculiar filling system adopted by Moore for its Non-Leakable pens, for which three distinct patents were filed, one in 1893 (nº US-501895) and two in 1896 (nº US-567151 and nº US-567152). The principle is always to use a recessed nib assembly, but in this case instead of using a helical screw, there is a linear sliding type.
The system has, compared to the traditional safety filler, the advantage of an enviable mechanical simplicity, in this case in fact the sliding of the nib group is achieved through the use of a sleeve placed on the bottom of the pen that is made to slide back and forth on the shaft of the same. At the bottom that closes the sleeve is hooked with a rod the nib group, which emerges through a gasket watertight from the bottom of the barrel, so it can be moved into writing position or returned to the body of the pen.
With the nib in the retracted position the pen can be loaded or closed like any other traditional safety, so much so that Moore sold its own pens leaving the factory already loaded with ink, as further evidence to support the actual truthfulness of their name Non-Leakable.
The mechanical simplicity of the system, based on the simple linear sliding of a rod, is the strong point of this mechanism, much more robust and easy to made compared to the complexity of that used in the other retractable pens; all that was required was a good precision in the tolerances of the mechanical machining and good quality gaskets.
In addition to the Moore the system was also used by the Montblanc in their first Rouge et Noir models, almost certainly brought to Germany for the foundation of the company by Arthur Eberstein, who had previously worked for the Moore.
security eyedropper
This "system" was found almost exclusively on Japanese pens, and can be considered a variant of the plunger filler of the Onoto, from which it was probably inspired. On a mechanical level, in fact, the mechanism is essentially identical, but in this case it is not used to fill the pen, but only to block the flow of ink to the nib when the pen is closed. It is not known an inventor of this mechanism, that it is found on around all Japanese pens produced until the years '30 from companies like the Pilot and the Sailor.
The pen is filled by unscrewing the nib group and inserting the ink directly into the body of the pen, as for the ordinary eyedropper filler. However, to avoid possible losses, which would be disastrous for the traditional clothing of the Japanese (the kimono), the pens equipped with this system are equipped with a piston mounted on a shaft operated through the bottom of the pen. When the bottom is screwed on, the piston, which serves exclusively as a blocking valve, comes into contact with the nib group, blocking the access of the ink to the same, so as to prevent any possible leakage.
In order to write it is necessary to unscrew the bottom and slightly withdraw the shaft attached to it, so as to retract the piston from its blocked position and re-enable the flow of ink towards the nib. Closing the bottom will stop the ink flow again, thus preventing leaks.
Direct compression of the sac
At the beginning of the 1900's, there was a great impulse in the search for a system that would allow the filling operation to be carried out automatically. During this period, a series of filling systems began to be produced, in which the ink was kept inside an elastic rubber sac. In this way it was possible to carry out the loading by compressing the empty sac, so as to exploit the subsequent expansion of the same to suck the ink from the bottle by immersing the nib assembly.
The idea of using a rubber sac as an ink tank helped to solve some of the problems encountered until then. In particular, since the ink was no longer in contact with the material of the pen barrel, it was also possible to use materials that were susceptible to corrosion. Moreover, if the rubber tank is well positioned and is not placed in contact with the walls of the drum, the layer of air that separates it from it acts as thermal insulation, and the elasticity of the bag compensates for the problem of increased pressure due to the heat transmitted by the hand that holds the pen.
However, there are also drawbacks: first of all, the size of the tank decreases, since the space inside the barrel of the pen must contain it, along with all that is necessary for the compression system. Moreover, the sacs tend to deteriorate, breaking or losing their elasticity, and must be replaced, thus introducing a whole series of maintenance problems. Finally, the complexity of the construction increases considerably, and with it the possibility of failure.
In this second section we have collected all the simplest and most primitive filling systems that provide some form of mechanical compression action performed directly on the rubber sac, or better, on the so-called pressure bar a metal bar that is placed (or glued) on the sac to allow you to apply the compression to it in a uniform manner.
crescent filler
The first truly efficient and functional automatic filling system based on the compression of a rubber tank was the famous crescent filler, designed by Roy Conklin' who patented it in 1901 (nº US-685258), which was introduced to the market by the company of the same name founded by him, the first example of the success of a brand due to the invention of an innovative filling mechanism.
The crescent filler is based on the realization of a particular pressure bar on which a metal crescent shaped bow is welded (from which derives the name given to the system by its inventor). The bow comes out of the body of the pen through a side slit made on the shaft of the same. By pressing on the headband you can directly compress the sac and thus quickly and easily fill the pen.
To avoid accidentally pressing the crescent filler the pens were also equipped with a ring retainer that went to fit into the slot under the bow, so that it was locked in an open position outside the pen. When it was necessary to load the pen it was enough to rotate the ring, cut on one side, to bring the position of the cut in correspondence of the slit, so that the bow could go down.
The system was simple and effective, and also allowed for better filling than the later lever filler, as the rubber tank could be completely compressed. Despite its technical superiority, however, the projection of the bow from the body of the pen was quite unpleasant from an aesthetic point of view, and this decreed its inexorable decline.
match-stick filler
The match-stick filler system is one of many systems designed at the beginning of the century to try to automate the fountain pen ink filling. In this case it was a matter of compressing the rubber tank through the use of a match (or a toothpick or other similar tool) that went to press, through a hole made on the shaft of the pen, on the compression bar.
The problems of this mechanism were mostly related to providing adequate positioning to the pressure bar (it was usually glued). The system was not particularly sturdy, nor elegant, and it assumed however the possession of a match, without which it turned out useless. To this problem some producers had obviated making the clasp dismountable and usable to the place of the match, or creating an opportune protuberance on the head of the cap or using some alternative form in order to furnish an adequate partridge.
The system is therefore quite primitive since no one had found a solution to its most important problem, that in case of breakage of the inner rubber bag, the ink could escape from the hole on the body of the pen with the imaginable unpleasant consequences.
coin filler
The coin filler is a variant of the previous match-stick filler system in which instead of a match the user pushes directly on the pressure bar using a coin or a medal or similar object, often elliptical in shape to allow a smaller width of the slot made on the pen body. Also in this case, in fact, the pressure is exerted through a lateral opening made on the barrel of the pen.
The drawbacks are substantially the same of the match-stick filler, soothed from the fact that a coin is an object generally more common, and it is not necessary to be a smoker. The larger size of the slit on the body, however, made the pen less elegant and more prone to problems. Often the slit is identifiable with respect to the case of a toggle pen in which the latter has been lost, by the presence of an additional round central hole slightly larger than those of the slit.
The system was used by Waterman in some models between 1913 and 1914, which were sold with a special coin. The scarce practicality of the system led to the disposal in less than a year, which makes these pens (that sometimes can be confused with later models with lever, but missing the same) rather rare. But even rarer and much sought after by collectors, are the coins supplied with the pen, since most of them were lost.
pull filler
Thepull filler, also called the collar filler, is a filling system that dates back to around 1906 (the patent is nº US-804847 applied for in 1905), when Holland, then still one of the most important manufacturers of fountain pens, introduced a model that used it.
The system, clearly influenced by the crescent filler of which it is essentially an alternative, involves the presence of a metal rod that covers about half the diameter of the body of the pen, connected internally to a pressure bar located on the opposite side of the inner rubber tank.
By pulling the rod (called the collar, from which the other name of the system) you compress the rubber tank and thus allow the filling of the pen. As you can easily guess, the mechanism is substantially similar to the crescent filler, with the advantage of protruding less from the side of the pen, but still remains not too pleasant on the aesthetic level.
sleeve filler
The sleeve filler, also called thumb filler, is one of the many filling systems experimented at the beginning of '900, in particular it was adopted by Holland around 1905 and by Waterman that used it from 1910 to 1915. This loading system is based on the displacement of a sleeve that wraps the barrel of the pen to hide a large opening made on one side of it. Moving the sleeve, which protects the opening, gives direct access to the pressure bar (on which a relief button was usually mounted at the opening), which can be so pressed using the fingertips.
The presence of the sleeve that wraps around the barrel at the opening, however, makes the size of the body of the pen uneven, which are therefore often unpleasant from an aesthetic point of view. Moreover, the mechanical complexity of the pen and its general fragility are greatly increased, since the pens of that period were made from hard rubber, a material not particularly resistant to mechanical stress. For this reason this filling system had a reduced diffusion and was soon abandoned.
A second version of this filling system, much more sophisticated, was adopted by LeBoeuf in 1930. In this case it didn't have a sleeve, but it was the whole barrel of the pen (made this time in celluloid) that could be unhooked from the nib group, sliding on an inner cylinder made of metal, on which there was lateral opening for the direct pressure on the sac. In this case, a uniform cylindrical shaft was obtained that had no lists, not even for the housing of the lever.
In a similar form, at least on an aesthetic level, this loading system was adopted also by the Parker for the aerometric used in the 51 (which, however, provides for multiple pressures for the presence of a breather), while a substantially identical system is still used today by some converter (for example those of the Pilot low end fountain pens).
hump filler
The hump filler is basically a variation on the theme of the crescent filler in which the sac is compressed using a protruding element from a side opening of the pen. The element allows you to compress directly the rubber sac, the main differences between the variants of this filling system are the ways in which it ensures, more or less reliably, that the protrusion can not be pressed accidentally.
The system had some diffusion at the beginning of 1900, as an alternative to the success of the Conklin crescent filler, one of the best realized versions was the so-called Wawco filler conceived by William Welty (patent nº US-834542) and used for the pens produced by the latter both with the Wawco brand and with the other brands used by the company.
Lever fillers
Below are the main loading systems used by the various manufacturers throughout the long history of the fountain pen from its origins to the present day. Many of these systems were born as an attempt to circumvent the original patent of Sheaffer, or to find alternatives that could distinguish the pens that used them compared to the competitors.
The principle of these loading systems always remains that of compression, and subsequent expansion to suck the ink from the bottle, of a rubber sac; therefore, the general considerations on advantages and disadvantages made in the previous paragraph apply. The substantial difference is in the mechanism with which the compression is carried out, however also in this case it is generally made use of a rigid pressure bar, pressed by the mechanism of the lever, to distribute uniformly the pressure on the sac.
lever filler
The lever filler is probably the filling system most common among vintage pens (and has also been used, as a form of revival, by some modern manufacturers). Introduced massively to the market in 1912 by Sheaffer, who has always proclaimed its invention, it has been produced in countless variations and versions, many of which, often technically inferior, have been created only to circumvent the patent (nº US-896861) that covered the invention of Walter Sheaffer that originated in 1908.
In fact, the ancestry of Sheaffer is seriously under discussion; in fact, there are previous versions of this loading system, a Swedish Johansson patent from 1898 and an American Barnes patent (nº US-726495) from 1903, the presence of which has allowed other companies, such as Waterman, to use variants of the same system. However, the success of the system and its enormous diffusion can be attributed to the massive investments of Sheaffer.
In the case of the Sheaffer patent the mechanism involves the compression of the sac using a lever that press on an elastic metal bar (the so-called spring bar) shaped like a "J", this one is inserted in the body of the pen with the curved part towards the bottom so as to make to adhere the straight part on the barrel of the pen, in correspondence of the lever. In many cases the pressure on the sac is not directly exerted by the spring bar that is hooked to a pressure bar which is the one that is pressed against the bag.
In the rest position the lever is placed horizontally in a slot in the side of the pen body. In the original version of Sheaffer it was held in place by a thin metal pin that crossed it centrally, inserted directly into the shaft of the pen, which was drilled for the occasion. Lifting the lever from one side the other side pushes down the pressure bar, which thus compresses the sac.
As mentioned above, there are several different versions of this mechanism. For example, Waterman, in order to circumvent Sheaffer's patent, introduced, based on Barnes's patent, a lever pivoted directly inside a metal cage that contained the entire mechanism. This in turn was fixed with fins to the pen, using as housing a special slit created in the barrel side.
A more efficient system, later used by other producers (including Sheaffer, but only after patent expiry), requires the lever to be held in place by a metal ring through it (patent nº US-1292736). This is inserted inside the pen and maintained in position by means of a special groove, made internally on the barrel in correspondence with the lateral opening from which the lever itself is housed. This system has the considerable advantage of greater mechanical strength, since it does not require drilling holes for the pin in the material of the barrel, which in ebonite pens was often quite fragile.
Other variations of the system concern the way in which the lever exerts pressure on the sac: for example the Eversharp did not use a flexible bar but a flat bar with the sides folded like a "U", anchored on a hook on the bottom of the pen. The lever was equipped on the external end with two tips that went to fit in the rail obtained from the folding of the bar, so as to raise it to the rest position after filling, furthermore to keep the lever locked in the rest position, it was equipped with small protrusions that went to fit into special recesses created in the housing slit.
The Conklin with the Endura introduced a version in which only half of the lever being lifted was exposed externally, reducing the size of the slit on the barrel. Moreover, the mechanism used by Conklin, like that one of Eversharp, did not use a spring bar, but a pressure bar was stuck directly to the lever by means of two small hooks inside it, which went to fit into a special hook on the bar.
Another noteworthy variant of the system is the one of Carter, derived from a patent (nº US-1209978) of the De Witt-La France, which has a sort of "leash" attached to the lever that prevents it from tipping over once it has reached the vertical position, in order to avoid damage to the pen and the system.
Finally, a particular version is the one of the Eversharp Skyline, which could also be classified as a breather tube filler. In this case, in fact, inside the rubber sac there is a breather tube, and the spring bar is very short and aimed at compressing only the final part of the bag. The pen is loaded by repeating the pressure action several times with the lever, using the classic principle of the breather tube filler. Similar to this, even if realized in a completely different way, is the Waterman Ink-Vue.
spoon filler
The spoon filler owes its name to the shape of the bar used to compress the tank, which is similar to that of a spoon. In this case, the pressure is exerted on the enlarged end of the spoon, which is accessed by unscrewing a blind cap placed on the bottom of the pen barrel. The bar is properly hinged to the bottom of the barrel, so that the pressure on the spoon, moving the internal section of the bar, causes it to press on the sac.
Various companies have used this type of loading, such as Columbus, which patented a version in 1929 (nº GB-334913), but in general it introduces unnecessary mechanical complexity and greater stress on the materials of the pen, without providing any particular benefits. It has been adopted mostly as an attempt to circumvent patents on lever filler, or as a sign of distinction with respect to other mechanisms, as it avoids the side slit for the lever, but has never been a significant success.
hatchet filler
In reality two completely different filling systems are called hatchet filler, as they were given this name by their respective manufacturers. The first is the one used by Holland from 1908 to 1912. The filling always involved the use of a pressure bar placed at a slit, except that in this case the slit was left open on one side, while on the other side a 'P' shaped lever was placed.
The lever was hinged on one of its extremes (the stem of the "P") at the end of the slit, and returned with the protruding part inside the body of the pen, on the bottom of the same. For the filling the lever was extracted and tilted of 180°, to be able to go to press on the pressure bar using the protruding part; once brought the lever in position of pressure in substance the mechanism becomes analogous to the crescent filler, with the advantage of not having protruding sections (but with the disadvantage of a certain fragility and mechanical complexity).
The second system is the one used by Crocker around 1910, in this case the bottom itself is anchored to a lever, which raised in a vertical position compresses the sac. To be used the bottom was unscrewed, after which the lever could be operated. Holding it screwed in, the lever was locked in the rest position, thus avoiding accidental pressure.
Both of these systems can be counted among the various attempts to create a bag compression system based on mechanisms that differed from those patented by other manufacturers. Given the relative complexity and the low technical efficiency, both have not had any significant follow-up. Their rarity, however, makes them interesting from a collector's point of view.
bottom lever filler
The top lever filler is a particular lever filling system used by Aurora from around 1930 for the Internazionale model, and later also on the Novum. The first version of this filling system however, was used by Curzon for the Top Lever model (later renamed Debrett's) of 1926. Since the patent of the Top Lever (nº GB-273357 and nº FR-628272 which is even more similar to the mechanism found on the Aurora) is from 1926, it is incorrect to attribute the invention of this system to the Aurora. There are no other known variants of the system used by other manufacturers except the switch filler of the Pilot, which has some similarities, in particular with the variant of this system adopted later on the Superna model.
In essence the top lever filler creates a sort of combination between the principle of the lever and the mechanism used in the button filler. In this case the lever is very short and positioned on a slot made on the bottom of the pen, the lever must be raised from its resting position, in which it is folded inside the bottom, and at that point pushing it further you go to operate an internal pressure bar similar to those used in the button filler, which arching compresses the sac.
The system is rather complex and delicate (given the small size of the lever the efforts to be applied are greater), and to avoid deforming the body of the pen Aurora inserted a reinforcement inside the same (made with a thin metal cylinder of aluminum inserted on the inner surface) that further reduces the space available for the sac.
The mechanism allows to avoid the presence of the blind cap of the button filler, and the related problems of loss, at the cost of a certain mechanical complexity. Its main purpose, apart from distinguishing itself from other manufacturers, however, it is mainly to aesthetically pleasing avoiding a gap on one side of the pen.
A variant of the system, also introduced by the Aurora with the Superna model, involves the mounting of the bottom lever in a vertical position; the lever is mounted inside an aluminium structure inserted in the bottom of the pen, which takes care to absorb the stresses. The lever emerges from a hemispherical shaped dome and can be operated by means of a plastic ball placed on the external end. In this case, the mechanism is accessed by unscrewing the bottom blind cap and charging the pen by pushing the lever through the ball.
Sac mechanical compression fillers
This section brings together all the other loading systems based on the mechanical compression of a rubber sac, but carried out by means of a mechanical system that does not refer directly to the lever principle, and therefore used as a legally conclusive alternative to the system introduced by Sheaffer.
button filler
The button filler was introduced by Parker in 1913.[2] The system was born from the need to find an alternative to the Sheaffer lever filler not copying the design thus avoiding all possible legal problems due to patents.
In this case, the system requires that the compression of the rubber sac is carried out through a flexible metal strip (often called "I-bar") that is curved by pressing it with a button on the bottom of the pen. The strip in the rest position is straight and resting on one side of the pen body. On the underside it is placed in contrast with the nib assembly (in some cases a special recess is created on the body itself). On the upper side it comes out, through a curved end, from a hole made on the bottom of the pen, and inserted into a metal button.
Pressing the button causes the rod to bend towards the center of the pen, causing the sac compression. Again, a pressure bar is used to make the sac more evenly compressed. The advantage of this system is that there is no need for a side slit in the pen body. The fact that the access to the button was protected by an screw-on blind cap allowed to affirm a greater security than the loss of ink in case of breakage of the bag, also the system was promoted for its ability to allow the loading of the pen with one hand.
In fact, in addition to the previous advantages, this system also has some disadvantages. First of all, the system is more cumbersome and requires a good positioning of the flexible strip, also the filling capacity is limited, not being able to have the button a large excursion, and thus obtaining a flexion, and consequent compression, limited. Finally, pressing the button requires a certain amount of effort.
Nevertheless, the system was quite successful and was reused by various European manufacturers. In particular, an interesting variant is the push-knob made by Montblanc, in which the blind cap itself serves as a button. In fact, it can be partially unscrewed until it is brought into a position where the internal button on which the metal spring is anchored is hooked, pressing the blind cap compresses the spring and loads the pen. Once filling is complete, the blind cap can be returned to the locked position to avoid accidental pressure.
Another variant is the one patented by Soennecken in 1930, which provides for an ebonite button hidden by a shell by rotating which you can reach the loading button and operate it, while rotating it in the reverse direction this is returned to the original position, blocking access to the button. Both variants make it possible to overcome another not insignificant problem of the classic version, which is the not insignificant probability of losing the blind cap.
twist filler
As its name indicates, the twist filler is based on the compression of the reservoir through the exercise of a torsion on it. In this type of filling in general the tank is made not with a sac, but with a rubber tube whose rear end is glued to the bottom of the body of the pen that can be rotated, so as to generate the twist that literally "squeezes" the same.
Although it has some advantages compared to the traditional lever filler, such as greater mechanical simplicity and the aesthetic merit of not needing a lateral opening on the body of the pen, the main defect of this system, which decreed its substantial failure, was the greater ease with which the rubber tank could break due to the considerable effort imposed on it by the torsion.
The system was mainly used by A. A. Waterman who around 1902 acquired a patent (nº US-744642, attributed to Harry W. Stone) relating to it. Other companies introduced similar systems, or inspired by the same principle of rotating the bottom of the pen to squeeze the tank, such as the leverless of the Swan. A very particular version of this type of loading was used on a prototype pen of the Nettuno never marketed.
leverless filler
The leverless filling system was adopted by Swan in 1932 for the models of the same name, and its use was mainly dictated by aesthetic reasons. It is essentially a variant of the twist filler in which however the tank is realized with a rubber bag as in the ordinary lever loading and the comprehension torsion happens through an eccentric bar anchored to the bottom of the pen that in position of rest remains lateral, whose rotation involves a torsion applied laterally to the bag with the relative wringing.
Compared to twist filler the substantial innovation introduced by Swan was to allow only a limited rotation of the bottom, marked with arrows, and avoids excessive stress applied to the rubber of the bag. The system however had a limited success and has been used only by this company, having in substance the same problems of fragility of its analogue and a rather reduced filling capacity.
switch filler
This is how the filling system adopted by the Pilot for its Super line is called, by the shape of the knob that activates filling. As can be seen from the relevant patent (nº US-2871825), this is a system based on the same principle as the button filler, in which a I-bar is flexed by actuating a sort of switch at the bottom of the pen. The system is very similar to the bottom lever filler of the Aurora, in particular to the variant with ball used on the Superna; unlike this, however, the operation is done by removing the shaft of the pen to access the internal mechanism.
Pneumatic fillers
This section classifies loading systems based on the pneumatic compression of a flexible rubber sac. The latter is compressed by the atmospheric pressure generated by the filling system to release the air that will be replaced by the ink during the decompression phase, when the sac returns to its normal size due to its elasticity.
blow filler
The first working version of pneumatic loading can be considered the blow filler created by Seth Sear Crocker in 1901 (nº US-678547). The system was very simple both in terms of operating mode and construction, but it was really very uncomfortable to use.
In the blow filler indeed the pneumatic pressure is generated directly from the user of the pen that must blow (from this the name comes from) inside the barrel through a special hole drilled on the bottom of the same. The pressure thus generated compresses the internal sac and allows the subsequent filling of the pen.
Obviously to be able to use the blow filler you need good lungs to be able to blow with force, and you need to do so in a position where the pen has the nib immersed in the ink, which makes this filling system anything but comfortable. For this reason the pens were also supplied with a pump to be used as an aid for filling.
Because of its poor convenience the system had a short life and was used exclusively by the Crocker, who still looked for alternatives with its hatchet filler, but from it derives the Chilton pneumatic system made by the son of Seth Crocker, which although being one of the most original and effective systems ever made, did not have the success it deserved.
pneumatic filler
In 1924 Seth Chilton Crocker resumed the idea of the blow filler invented by his father Seth Sears Crocker, further refining it using a new patent (nº US-1528379, by David J. La France). The new system was based on the fact that the body of the pen slides around a metal tube screwed on the nib assembly to which was mounted the classic rubber sac to compress. To perform this action, the outer barrel of the pen could slide on the inner barrel and the watertight seal between the two was made by a waxed wire placed at the end of the inner metal cylinder.
The outer barrel of the pen had, as for the blow filler an aeration hole on the bottom. The filling was obtained by sliding back the body of the pen and then bringing it back into position by keeping the hole in the bottom closed with a finger. In this way the pressure generated on the sac causes its compression, but once left free the aeration hole the subsequent expansion of the sac causes the suction of the ink.
The system was simple, functional and sturdy, all the space included in the inner barrel was usable for the bag (without the need for a pressure bar as for lever filler) which allowed the Chilton to have a much higher autonomy than the competitors. Moreover this simple mechanism was very easy to repair, it was enough to unscrew the inner barrel to replace the sac. Finally, the presence of the aeration hole allowed to keep balanced the internal pressure of the pen, so that it did not present problems of leakage or absence of ink in case of variations in pressure or temperature.
Simplicity was a strength of the Chilton, the outer barrel was not even anchored to the nib assembly, as this was not necessary because for the mechanical precision of the machining it did not flow during use. The only drawback was that to work the pen required a longer nib assembly length to handle the pen once the body had been retracted for fillig, which had to be done with two hands. Since the thread for the cap was placed on the outer barrel of the pen (so that it was locked when the pen was closed), this also meant a longer cap length, and therefore an unproportionate appearance.
For this reason in 1927 was created a second version of the filling system, in which the outer barrel was anchored conventionally to the nib assembly, and in its place was used to generate depression a second metal tube placed between it and the inner barrel. The depression system was anchored to the bottom of the pen which was a blind cap, in this way it was sufficient to unscrew the bottom of the pen to perform the loading, which at this point could be performed with one hand.
The Chilton however does not seem to be the only manufacturer to have used this system, in fact a substantially identical system called Compressor was invented by Montblanc in 1923 (patent nº DE-400356) and used from 1924 to 1929 for some models, which however were marketed on a small scale (mainly in France) and did not have a significant success.
Touch Down
The loading system called Touch Down by the company itself was introduced by Sheaffer in 1949 for the namesake models, and is nothing more than a more sophisticated reworking, carried out after twenty-five years (patent nº US-2610612), after the Chilton pneumatic filler system, whose patent (nº US-1528379) is mentioned explicitly. In fact the operating principle is essentially identical, what changes is the way in which the pneumatic compression of the rubber sac inside the pen is carried out.
Also in this case there is an unscrewable bottom that is hooked to a metal cylinder that slides hermetically thanks to a gasket along the body of the pen, the mechanism is however much more complex to avoid the use of the ventilation hole on the bottom of the pen and allow compression only by pushing down the tube anchored to the bottom once you have extracted it.
In this case, the compression takes place by passing the air in the cavity through not a hole on the tip of the cap but short lateral grooves at the two ends of the inner tube. When opening the grooves on the bottom allow the expansion of the bag, closing the piston the slide is sealed and the internal air compresses the sac, at the end of the course the other grooves allow the air to escape and the expansion of the sac loads the ink.
snorkel
The filling system often referred to simply as snorkel (although this is only one of the components) was introduced by Sheaffer in 1952 with the Snorkel Pen. The system represents an evolution of the previous Touch Down, and the filling mechanism in fact is exactly the same, and uses a pneumatic compression realized in the same way.
The novelty is not so much the way in which the ink is aspirated as the fact that in this case it is no longer necessary to fill the pen by dipping the nib inside the bottle. During the opening phase, in fact, it is possible to extend through the feeder a small metal tube (the snorkel) with an aeration duct that allows the passage of the ink through it instead of through the nib.
It is undoubtedly one of the most complex (and in some ways fascinating) filling systems ever used, which allows you not to dirty the nib and for this reason it was widely publicized. The main disadvantage is the capacity, generally in fact the loading unit that contains the sac is quite small and the pen contains little ink.
Breather tube fillers
These filling systems have in common the use of the presence of a breather tube which allows to perform the refill by repeating several times some mechanical action (different depending on the different filling systems) which allows to create a compression of the air inside the pen tank. The variety of ways in which this compression is carried out has been extremely wide, but in most cases provides some mechanism that acts on a flexible bulb, even if there are alternative mechanisms, such as the one found on some Ancora Lusso in which the depression is done with a very short running piston.
The breather tube is inserted in the feeder and kept in a central position with respect to the body of the pen, which normally acts as a tank. During the compression phase, the air in the pen comes out of the blowhole, from which, due to the depression created, the ink that ends up in the tank is loaded; the presence of the blowhole means that the ink loaded is not expelled in the subsequent compression phases, until the entire tank is filled up to the level of the blowhole.
The presence of the breather tube in some realizations also has a second positive effect because it allows to immediately balance the pressure of the air inside the pen body with that of the external air, since in this case the breather provides a way of communication between inside and outside, thus avoiding the various problems of leakage of the ink in case of pressure changes.
bulb filler
The bulb filler is probably the progenitor of all filling systems based on the presence of a breather tubes. Its origins are uncertain, one of the oldest patents (nº US-802668 of 1905) was granted to the Aikin Lambert, but there is an earlier one (nº US-723726 of 1903) that does not seem to have been used. But beyond the precursors one of the first models to have been massively produced and marketed is certainly the one of the Postal of 1925, although the most sophisticated version probably remains that of the Stylomine 303. Later the same system was also adopted by Eversharp for the Bantam model and for the stenographer-centralist version by Doric, and by Pelikan for the Rappen.
The system involves the direct use of the pen barrel as a reservoir, also allowing, when this was made of transparent material, the visualization of the ink level. Filling is carried out by pressing a rubber pump, similar to that of a dropper, inserted directly on the bottom of the body of the pen, and which can be accessed by unscrewing the bottom of the pen. Given the need to have a pump of sufficient size, this generally involves on this type of pen a much longer blind cap than that used on other filling sistems, such as the button filler or the piston filler.
The filling principle derives from the dropper principle, the pen tip is immersed in the ink and the pump is pressed, its expansion causes a depression that causes the ink to flow into the body of the pen. The innovation created by this filling system consists of the presence of the breather tube connected to the nib unit and directly connected to a duct in the ventilation hole of the nib.
This allows you to repeat the pressure on the pump several times, to perform different filling actions and progressively fill the pen. In the absence of the breather tube in fact, with the compression of the pump, the ink present in the barrel would escape, since there is no vent for the air contained in the same, thus obtaining a very limited capacity; the breather tube instead provides a way out to the air present in the tank that is compressed by the pump, and a way in for the ink that is sucked in by the depression. In this way it is possible to repeat the compression of the pump and continue to load ink until the latter does not exceed the level of the breather tube, completely filling the pen.
vacumatic
Introduced by Parker in 1933 with the launch of the Vacumatic model, it was advertised as the first rubber sacless filling system. In fact this is absolutely not true (a classic example of misleading advertising) both because at the time there were already several versions of rubber sacless filling systems, such as the plunger filler of Onoto and the piston filler of Pelikan, or because in reality the filling always relies on a flexible rubber element, the diaphragm, even if this does not perform the functions of a tank.
Among the various filling systems based on the use of a breather tube, the Vacumatic is certainly one of the most complex, but in reality it is only a reworking of the mechanism of the previous bulb filler in which instead of using a pump the compression of the air in the body of the pen is done through the movement of a rubber membrane, the diaphragm precisely. In this case the movement is made by pressing a spring button on the bottom of the pen, which acts on the mechanism that moves the membrane. Repeating the pressure several times results in the same pumping result as a normal rubber pump.
This mechanism has the advantage of having a shorter bottom, which makes the appearance of the pen more pleasant, this was even more evident in the first versions of the system, called "lockdown", in which the button, made with a metal cylinder with a lateral groove, could be kept in pressed position thanks to the presence of a "L" shaped end of the groove itself, which allowed it to be attached to the mechanism by a rotation, so then to allow the closure of the back itself (screw).
A second version of the system, called "speedline", was produced starting from 1937, in which the realization was simplified by eliminating the locking system. This involved a longer bottom, but was advertised for the possibility of filling with one hand (in fact, to unscrew the bottom you still use two). Since 1942 about the system was further revised (with the version called "wartime" by collectors) using a button in celluloid instead of aluminum.
aerometric filler
It was introduced by Parker in 1948, as a new filling system adopted on the 51 in place of the previous vacumatic. Actually for the operating modes this system is very similar to the sleeve filler used by LeBoeuf, because it is based on the pressure of a rubber sac to be made by a side opening on the metal cylinder that contains the same, which is accessed by unscrewing the pen body from the nib section.
Unlike the classic sleeve filler the aerometric filler however provides for the presence of a breather inside the system, which requires to repeat the pressure of the bar four or five times (as shown on the instructions engraved on some of them) to complete the loading. It can therefore be interpreted as a fusion between a sleeve filler and the previous vacumatic filler.
The name aerometric is actually used in this sense mostly by collectors, the company was rather referring to it by the name Aero-metric Ink System (reported for example in advertisements like this) for the set of the filling system (called Foto-fill filler), the feeder and the new PVC tank (called Pli-glass), which allowed the company to proclaim the pen as not containing any rubber parts.
stantuffo tuffante
The "stantuffo tuffante" is the name given to the filling system invented and patented by OMAS in 1936 with the introduction of the Lucens model. In reality, a loading system substantially identical to this and equally functional is found on the pens made by Dunn dating back fifteen years. For this reason, even if we cannot establish or not the originality of the invention of the OMAS it is not however correct to assign to it the complete paternity of this type of loading, even if today in Italy we refer to it with the name of "stantuffo tuffante" for the greater notoriety achieved by the Lucens compared to the pens of the Dunn and for the fact that it had not given a specific name to its loading.
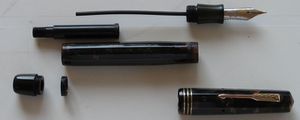
The principle of operation remains that of all breather tube filling systems, except that in this case the pressure inside the body of the pen is exerted through a hollow piston which is accessed from the bottom, which has an extended end part, but perforated at the center so as to be able to flow abundantly around the breather tube, which in this case is very long and comes close to the end of the pen.
Unscrewing the bottom, it is possible to extract the cylindrical piston, which slides tightly with respect to the body of the pen, and to carry out the pumping action through it. The mechanism is very functional and clearly more advanced than the vacumatic and other similar systems because unlike that it does not require membranes or other flexible rubber elements, and has a greater mechanical simplicity. The disadvantage is the slightly larger size of the mechanism.
Although it is one of the most advanced, effective and interesting filling systems, which has all the advantages of other breather tube systems and none of the problems related to the presence of flexible rubber membranes, the "stantuffo tuffante" unfortunately had a low diffusion, which sees it limited in its use to the Dunn pens and the aforementioned model Lucens of OMAS.
Ink-Vue filler
Visofil filler
accordion filler
Vacuum fillers
This group brings together all those systems that require that the filling takes place through the creation of a depression inside the body of the pen so that the ink is sucked through it. In this case it is generally the body of the pen itself that acts as a reservoir, and can be made of transparent material so as to allow the visualization of the ink level.
As with other systems that use the pen body as a reservoir, this also has the advantage of having a greater volume to contain the ink, but the disadvantage is that the residual air contained in the reservoir is sensitive to changes in temperature, which makes it easier, due to the increase in volume in case of heating, the cases of leakage of ink, especially when the pen is almost discharged and the volume of air is greater.
pump filler
syringe filler
plunger filler
piston filler
Others
All the other filling systems have been brought together in the latter group, which have in common the fact that they do not have a common factor that allows them to be classified in a homogeneous manner.
capillarity filler
cartridge filler
converter
External references
- [1] Page of the original sketches used in this page
- [2] Page on filling systems from Richard Binder's website
- [3] Page on filling systems from David Nishimura website
- [4] Page on filling systems from Penspotters
- [5] Article about filling systems on PenTrace, first part
- [6] Article about filling systems on PenTrace, second part
- [7] Article of Jim Mamoulides on Parker's button fillers
- [8] Article on Penexchange on piston filler
- [9] Article on Penexchange on pneumatic fillers
- [10] Article on Penexchange on button fillers
Notes
- ↑ but the company has done so using many patents of Francis C. Brown of Caw's, which was the first brand to use it, albeit in a more primitive version.
- ↑ at least as reported on this story of the initial Parker models, the first Parker patents related to loading, nº US-1346045 and nº US-1486246, are respectively from 1919 and 1922, certainly after the introduction, since the Duofold is also from 1922 and the system also appears in this 1916 advertising, in this discussion however is reported the purchase by the Parker of the patent nº US-787152, which is from 1905.
Thanks
A big thanks to Fabio Moricci, the Pennaio, who kindly gave us the use of his sketches as a basis for the realization of the technical diagrams of the various loading systems.