Sistemi di caricamento
La creazione di nuovi sistemi di caricamento è sempre stata, specie negli anni del periodo d'oro dello sviluppo della penna stilografica, uno dei maggiori fattori di innovazione tecnica, e per questo anche ragione della nascita di nuove aziende; in questo campo gli esempi più famosi sono la Conklin, nata per l'invenzione del Crescent filler e la Sheaffer, che entrò sul mercato con la creazione del caricamento a levetta, ma molte altre aziende meno note (come la Onoto, la Dunn, la Moore o la Chilton) hanno avuto una simile origine.
La storia della penna stilografica è infatti indissolubilmente legata a quella dei vari sistemi che nel corso degli anni sono stati ideati per effettuarne il caricamento dell'inchiostro. In particolare nei primi anni del '900 tutti i produttori facevano a gara per introdurre nuovi sistemi di caricamento, spesso inutilmente complicati e poco funzionali, che poi venivano usati per promuovere la superiorità delle loro penne.
Si sono riportati qui di seguito i principali sistemi di caricamento adottati dai vari produttori nel corso della lunga storia della penna stilografica a partire dalle sue origini fino ai nostri giorni. I vari sistemi sono stati raggruppati per affinità di funzionamento, ed i vari gruppi sono presentati in un approssimativo ordine cronologico di introduzione.
Caricamento diretto
Si sono classificati in questo primo raggruppamento tutti quei sistemi di riempimento che prevedono il caricamento della penna attraverso l'immissione dell'inchiostro all'interno del corpo della stessa effettuata direttamente da parte dell'utilizzatore. Si tratta dei sistemi di caricamento più primitivi, utilizzati agli albori della storia della stilografica. Nella gran parte dei casi sono stati sostituiti a partire dagli inizi del 1900 da sistemi che consentissero il riempimento automatico.
Nei sistemi illustrati in questa sezione il corpo della penna svolge anche la funzione di serbatoio, e non esiste un meccanismo che permetta di automatizzare il caricamento dell'inchiostro, che in genere viene immesso tramite un contagocce; le varianti proposte attengono soltanto alle diverse metodologie utilizzate per dare accesso al serbatoio.
eyedropper filler
Il cosiddetto eyedropper filler, come viene chiamato nel mondo anglosassone, è quello che da noi viene denominato spesso caricamento a caduta oppure, con una traduzione diretta, caricamento a contagocce. Si tratta del primo sistema di caricamento adottato nelle stilografiche ed in realtà non lo si può considerare neanche un vero e proprio sistema di caricamento, dato che in sostanza non esiste nessun "sistema".
In questo caso infatti il riempimento della penna avviene smontando il gruppo pennino dal fusto, che essendo cavo viene utilizzato direttamente come serbatoio. L'operazione di riempimento viene effettuata, ottenuto l'accesso al serbatoio, con l'immissione dell'inchiostro a caduta da effettuarsi in genere con un contagocce, che nelle versioni originali veniva fornito dal produttore stesso assieme alla penna. Completato il riempimento il gruppo pennino doveva essere rimontato sul fusto per poter utilizzare la penna.
Per la sua semplicità costruttiva questo "sistema" è stato adottato da tutti i produttori fin dall'800 agli albori dello sviluppo della penna stilografica, ed è rimasto in uso fino agli inizi del '900. Il sistema è semplice, specie nei termini dei requisiti tecnici per la costruzione, ed inoltre ha il vantaggio di consentire una grande capienza di inchiostro, maggiore di qualunque altro, in quanto determinata solo dalle dimensioni del corpo della penna.
Presenta però numerosi inconvenienti, il primo dei quali è senz'altro la scomodità delle operazioni di riempimento, dato che per ricaricare una penna occorre smontarne la sezione con il pennino, in genere umido di inchiostro, e riporlo in luogo separato dove non macchi e non rischi di cadere. Le operazioni di caricamento poi sono molto scomode, occorre avere un contagocce o attrezzo similare, ed in genere l'operazione del travaso di inchiostro, dovendo mantenere sempre ben verticale il corpo della penna che agisce da serbatoio, risulta essere delicata ed a rischio di macchie e versamenti di inchiostro.
Un secondo inconveniente origina poi dal fatto che con l'usura, specie nei modelli di qualità inferiore, avere l'inchiostro in contatto diretto con il corpo della penna può causare perdite in corrispondenza della giunzione fra fusto e gruppo pennino una volta che questa perde la sua tenuta. Inoltre, dovendo svitare ed avvitare quest'ultimo il rischio di macchiarsi le mani, specie in presenza di un corpo che è stato pieno di inchiostro fino ad allora è sempre piuttosto alto. Il corpo della penna poi doveva essere realizzato soltanto in materiale inerte che fosse capace di resistere al contatto con gli agenti corrosivi presenti negli inchiostri, che all'epoca della sua introduzione era soltanto l'ebanite.
Un ultimo inconveniente, spesso molto fastidioso, è che essendo in questo caso l'inchiostro contenuto direttamente nel corpo della penna, quando questa si svuota si determina una notevole sensibilità alle variazioni di pressione e temperatura dell'aria contenuta all'interno del fusto della penna, che è tanto maggiore quanto più grande è il volume disponibile. I problemi maggiori si avevano allora in caso di viaggi in aereo, dove le variazioni di pressione altimetrica causavano invariabilmente una fuoriuscita di inchiostro.
Ma con queste penne per causare una perdita spesso è sufficiente il solo calore della mano che impugna la penna. Questo viene trasmesso all'aria contenuta all'interno del fusto, provocandone una espansione che altera così l'equilibrio della pressione fra interno e esterno. Si ottiene così con relativa facilità una perdita di inchiostro. Benché oggi sia tornato di moda in qualche modello, per il suo gusto retrò, resta comunque, posto che lo si possa davvero considerare tale, un sistema di caricamento primitivo.
safety filler
Il caricamento che nel mondo anglosassone viene chiamato safety filler, da noi tradotto in caricamento di sicurezza, nasce come evoluzione del sistema di caricamento a contagocce. Per semplificare le operazioni di riempimento evitando di dover smontare e riporre la sezione con il gruppo pennino, e per evitare fuoriuscite di inchiostro in conseguenza di differenze di pressione e temperatura, in questo caso il pennino viene montato su un meccanismo che consente di ritrarlo all'interno del corpo della penna. Da questa caratteristica viene anche il nome di rientrante con cui spesso si identificano le penne che usano questo caricamento.
Il sistema prevede che, fatto rientrare il pennino nel corpo della penna, quest'ultimo diventi accessibile per il riempimento, da effettuare tramite il solito contagocce, e con gli stessi problemi (escluso quello del riporre il gruppo pennino in luogo sicuro) visti in precedenza. In questo caso si ha meno volume disponibile per l'inchiostro, essendo l'interno del fusto occupato anche dal meccanismo, ma comunque sempre più che sufficiente. Per poter usare la penna basterà riutilizzare il meccanismo alla rovescia per riportare il pennino in posizione di lavoro, facendolo uscire dal corpo della penna.
Una volta che il pennino è rientrato all'interno del fusto, la penna può essere chiusa ermeticamente utilizzando un cappuccio a fondo piatto fornito di adeguate guarnizioni che permettono di garantirsi totalmente contro la fuoriuscita di inchiostro, caratteristica a cui è dovuto il nome safety con vengono chiamate le penne dotate di questo caricamento. In questo caso infatti non esiste la possibilità che l'inchiostro, a causa di scompensi di pressione, possa fuoriuscire dal pennino e depositarsi nel cappuccio, dato che quest'ultimo serve semplicemente come tappo per il fusto; tutti gli scompensi di pressione poi vengono immediatamente eliminati all'apertura del cappuccio.
Questa caratteristica di sicurezza fu un grosso passo avanti in un'epoca in cui le perdite di inchiostro erano molto comuni, e la tenuta dei cappucci, spesso bloccati semplicemente a pressione sul fusto della penna, era assai problematica. Da questo punto di vista le penne safety restano comunque superiori a qualunque penna moderna. Inoltre la chiusura ermetica del cappuccio, che comprende anche l'insieme del pennino, consente di ridurre praticamente a zero le possibilità di evaporazione dell'inchiostro, che molto difficilmente si seccherà all'interno della penna, consentendo così anche l'utilizzo di inchiostri molto più densi rispetto a quelli ordinari. Per queste caratteristiche peculiari la Waterman ha continuato a produrre una linea di queste penne, rivolta ad artisti e musicisti e aviatori, sino agli inizi degli anni '40.
Il fascino di questo sistema di caricamento risiede nella complessità meccanica della sua realizzazione, che spesso mostra i vertici delle tecnologie dell'epoca: il gruppo pennino infatti in genere viene fatto spostare grazie ad una vite elicoidale azionata dalla rotazione del fondello della penna. In posizione di lavoro esso andrà a chiudere ermeticamente il fusto tramite una guarnizione, mentre in posizione di riposo lascerà completo accesso all'interno della penna.
Con queste penne è fondamentale ricordarsi di aprire il cappuccio sempre in posizione verticale, e di non richiuderlo mai senza avere prima ritratto completamento il pennino all'interno del fusto, per evitare di danneggiarne la punta. Dato che questo era un inconveniente comune alcuni modelli (si attribuisce la prima introduzione di questa innovazione alla Montblanc) prevedono la presenza di un apposito meccanismo di sicurezza (in genere uno spillo montato al centro del cappuccio che va a battere sul gruppo pennino), che così ne impedisce la chiusura se questo non è stato completamente ritirato all'interno del corpo della penna.
Il safety filler nasce negli Stati Uniti nell'ultimo decennio del 1800, benché non sia possibile definirne in maniera precisa un inventore, se ne attribuisce se non l'invenzione almeno l'introduzione massiccia sul mercato alla Waterman, che è stato il principale produttore statunitense ad adottarlo su larga scala.[1] Esso però ha avuto un successo molto più grande in Europa, dove all'inizio del secolo praticamente tutti i produttori (ed in particolare quelli tedeschi, fra cui spicca la Kaweco, che ne realizzò anche alcuni sviluppi) facevano uso di questo sistema, e dove è rimasto in produzione molto più a lungo.
Benché lo sia classificato, forse ingiustamente, fra i sistemi di caricamento primitivi, in realtà il safety filler ha resistito sul mercato molto più a lungo di altri sistemi di riempimento creati in periodi successivi. In particolare in Europa si trovano in produzione modelli di serie che lo utilizzano fino al dopoguerra. A causa del suo valore storico, che lo vede essere sostanzialmente il primo sistema meccanico dedicato al riempimento della penna, esso continua a riscuotere un innegabile interesse da parte dei collezionisti, molti dei quali hanno una particolare predilezione per le penne rientranti.
non-leakable filler
Una variante degna di nota del sistema di caricamento di sicurezza è il peculiare sistema di caricamento adottato dalla Moore per le sue Non-Leakable, per i quali sono stati depositati tre distinti brevetti uno nel 1893 (nº US-501895) e due nel 1896 (nº US-567151 e nº US-567152). Il principio è sempre quello di utilizzare un gruppo pennino rientrante, ma in questo caso invece di utilizzare una vite elicoidale, si ha uno scorrimento di tipo lineare.
Il sistema presenta, rispetto al tradizionale safety filler il vantaggio di una semplicità meccanica invidiabile, in questo caso infatti lo scorrimento del gruppo pennino è realizzato tramite l'uso di un manicotto posto sul fondo della penna che viene fatto scivolare avanti ed indietro sul fusto della stessa. Al fondo che chiude il manicotto è agganciato con un'asta il gruppo pennino, che emerge attraverso una guarnizione a tenuta stagna dal fondo del fusto; in questo modo può essere spostato in posizione di scrittura o fatto rientrare nel corpo della penna.
Con il pennino in posizione rientrata la penna può essere caricata o chiusa come una qualunque altra safety tradizionale, tanto che la Moore commercializzava le proprie penne facendole uscire dalla fabbrica già cariche di inchiostro, come ulteriore prova a sostegno della effettiva veridicità del loro nome Non-Leakable.
La semplicità meccanica del sistema, basato sul semplice scorrimento lineare di un'asta, è il punto di forza di questo meccanismo, nettamente più robusto e facile da realizzare rispetto alla complessità di quello presente nelle altre penne rientranti; tutto quello che era richiesto era una buona precisione nelle tolleranze della lavorazione meccanica e delle guarnizioni di buona qualità.
Oltre che dalla Moore il sistema è stato usato anche dalla Montblanc nei primi modelli Rouge et Noir, portato quasi certamente in Germania alla fondazione dell'azienda da Arthur Eberstein, che in precedenza aveva lavorato proprio per la Moore.
contagocce di sicurezza
Questo "sistema" si trovava esclusivamente sulle penne giapponesi, e si può considerare una variante del caricamento a siringa rovesciata della Onoto, da cui probabilmente è stato ispirato. Sul piano meccanico infatti il meccanismo infatti è sostanzialmente identico, ma in questo caso non serve per caricare la penna, ma soltanto per bloccare l'afflusso di inchiostro al pennino quando la penna è chiusa. Non è noto un inventore di questo meccanismo, che si trova un po' su tutte penne giapponesi prodotte fino agli anni '30 da aziende come la Pilot e la Sailor.
La penna infatti si carica svitando il gruppo pennino ed inserendo l'inchiostro direttamente all'interno del corpo della penna, come per l'ordinario caricamento a contagocce. Per evitare però eventuali perdite, che sarebbero disastrose per l'abbigliamento tradizionale dei giapponesi (il kimono), le penne dotate di questo sistema vengono fornite di un pistoncino montato su un alberino manovrato attraverso il fondo della penna. Quando il fondello è avvitato il pistone, che serve esclusivamente da valvola di blocco, viene a contatto con il gruppo pennino, bloccando l'accesso dell'inchiostro al medesimo, così da prevenirne ogni eventuale fuoriuscita.
Per poter scrivere occorre svitare il fondello e ritirare leggermente l'alberino ad esso agganciato, in modo da ritrarre il pistoncino dalla sua posizione di blocco e riabilitare il flusso dell'inchiostro verso il pennino. Richiudendo il fondello si bloccherà nuovamente l'afflusso di inchiostro, prevenendo così le perdite.
Compressione diretta del serbatoio
All'inizio del '900 ci fu un grande impulso nella ricerca di un sistema che consentisse di eseguire in maniera automatica l'operazione di riempimento. In questo periodo si iniziarono a produrre una serie di sistemi di caricamento che prevedevano di mantenere l'inchiostro all'interno di un sacchetto di gomma elastica. In questo modo si poteva eseguire il caricamento comprimendo il sacchetto vuoto, così da sfruttare la successiva espansione dello stesso per risucchiare l'inchiostro dalla bottiglia immergendovi il gruppo pennino.
L'idea di usare un sacchetto di gomma come serbatoio per l'inchiostro consentiva di risolvere alcuni dei problemi riscontrati fino ad allora. In particolare non essendo più l'inchiostro in contatto con il materiale del fusto della penna si potevano utilizzare anche materiali suscettibili di corrosione. Inoltre se il serbatoio di gomma è ben posizionato e non viene posto in contatto con le pareti del fusto, lo strato di aria che lo separa da questo fa da isolante termico, e l'elasticità del sacchetto compensa il problema dell'aumento di pressione per il calore trasmesso dalla mano che impugna la penna.
Esistono però anche degli inconvenienti: anzitutto diminuiscono le dimensioni del serbatoio, dato che lo spazio interno al fusto della penna deve contenerlo, insieme a tutto quanto necessario per il sistema di compressione. Inoltre i sacchetti tendono a deteriorarsi, rompendosi o perdendo l'elasticità, e devono essere sostituiti, introducendo così tutta una serie di problematiche di manutenzione. Infine aumenta notevolmente la complessità di costruzione, e con questo le possibilità di guasto.
In questa seconda sezione si sono raccolti tutti i sistemi di caricamento più semplici e primitivi che prevedono una qualche forma di azione di compressione meccanica eseguita direttamente sul serbatoio in gomma. o meglio sulla cosiddetta pressure bar una barretta metallica (in italiano sarebbe chiamata barretta di compressione) che viene appoggiata (o incollata) sul sacchetto in modo da consentire di applicare la compressione sullo stesso in maniera uniforme.
crescent filler
Il primo sistema di caricamento automatico veramente efficiente e funzionale basato sulla compressione di un serbatoio in gomma è stato il famoso crescent filler, ideato da Roy Conklin che lo brevettò nel 1901 (nº US-685258), che venne introdotto sul mercato dalla omonima ditta da lui fondata, primo esempio del successo di una marca dovuto all'invenzione di un meccanismo di caricamento innovativo.
Il crescent filler è basato sulla realizzazione di una particolare barretta di pressione su cui viene saldato un archetto metallico a forma di mezzaluna (da cui deriva il nome dato al sistema dal suo inventore). L'archetto fuoriesce dal corpo della penna attraverso una fessura laterale praticata sul fusto della stessa. Premendo sull'archetto si può comprimere direttamente il serbatoio ed effettuare così in maniera semplice e veloce il riempimento della penna.
Per evitare di premere accidentalmente il crescent filler le penne erano inoltre dotate di un fermo ad anello andava ad incastrarsi nella fessura sotto l'archetto, in modo che questo fosse bloccato in posizione aperta fuori dalla penna. Quando era necessario caricare la penna bastava ruotare l'anello, tagliato su un lato, per portare la posizione del taglio in corrispondenza della fessura, in modo che l'archetto potesse scendere.
Il sistema era semplice ed efficace, e consentiva anche un caricamento migliore rispetto al successivo riempimento a levetta, in quanto si poteva comprimere completamente il serbatoio di gomma. Nonostante la sua superiorità tecnica però, la sporgenza dell'archetto dal corpo della penna risultava parecchio sgradevole dal punto di vista estetico, e questo ne decretò l'inesorabile declino.
match-stick filler
Il sistema di riempimento a fiammifero (o match-stick filler nella denominazione anglosassone), talvolta detto anche a stuzzicandenti è uno dei tanti sistemi ideati all'inizio del secolo per cercare di automatizzare il caricamento dell'inchiostro nella penna stilografica. In questo caso si trattava di comprimere il serbatoio di gomma attraverso l'uso di un fiammifero (o di uno stuzzicadenti o altro attrezzo analogo) che andava a premere, attraverso un foro praticato sul fusto della penna, sulla barretta di compressione.
I problemi di questo meccanismo erano per lo più collegati al fornire un adeguato posizionamento alla pressure bar (in genere veniva incollata). Il sistema non era particolarmente robusto, né elegante, e supponeva comunque il possesso di un fiammifero, senza il quale risultava inutile. A questo problema alcuni produttori avevano ovviato rendendo il fermaglio smontabile ed utilizzabile al posto del fiammifero, o creando una opportuna protuberanza sulla testa del cappuccio o utilizzando una qualche forma alternativa per fornire un adeguato pernio.
Il sistema pertanto risulta alquanto primitivo dato che nessuno aveva trovato una soluzione al suo problema più rilevante, quello per cui in caso di rottura del sacchetto di gomma interno, l'inchiostro poteva fuoriuscire dal forellino presente sul corpo della penna con le immaginabili poco gradevoli conseguenze.
coin filler
Il sistema di riempimento denominato coin filler in ambito anglosassone (che da noi potremmo chiamare a moneta) è una variante del precedente sistema a fiammifero in cui al posto di quest'ultimo si preme direttamente sulla barra di pressione utilizzando appunto una moneta o una medaglietta o oggetto similare, spesso di forma ellittica per consentire una minore larghezza della fessura praticata sul corpo penna. Anche in questo caso infatti la pressione viene esercitata attraverso una apertura laterale praticata sul fusto della penna.
Gli inconvenienti sono sostanzialmente gli stessi del precedente caricamento a fiammifero, leniti dal fatto che una moneta è un oggetto generalmente più comune e non occorre essere fumatori. Le maggiori dimensioni della fessura sul corpo rendeva però la penna meno elegante e più soggetta a problemi. Spesso la fessura è identificabile rispetto al caso di una penna a levetta in cui quest'ultima sia stata persa, dalla presenza di un ulteriore foro rotondo centrale di dimensioni leggermente superiori a quelli della fessura.
Il sistema venne utilizzato dalla Waterman in alcuni modelli fra il 1913 ed il 1914, che venivano venduti forniti di una apposita moneta. La scarsa praticità del sistema ne portò alla dismissione in meno di un anno, cosa che rende queste penne (che talvolta possono essere confuse con modelli successivi a levetta, ma mancanti della stessa) piuttosto rare. Ma ancor più rare e molto ricercate dai collezionisti, sono le monete fornite insieme alla penna, dato che la maggior parte di queste andava persa.
pull filler
Il pull filler, chiamato anche collar filler, è un sistema di caricamento che viene fatto risalire intorno al 1906 (il brevetto è il nº US-804847 richiesto nel 1905), quando la Holland, allora ancora uno dei più importanti produttori di stilografiche, introdusse un modello che lo utilizzava.
Il sistema, chiaramente influenzato dal crescent filler di cui costituisce in sostanza una alternativa, prevede la presenza di una barretta di metallo che copre una metà circa del diametro del corpo della penna, collegata internamente ad una barra di pressione posta sulla faccia opposta del serbatoio di gomma interno.
Tirando la barretta (chiamata collar, da cui l'altro nome del sistema) si comprime il serbatoio in gomma e si consente così il caricamento della penna. Come si può facilmente intuire il meccanismo è sostanzialmente analogo al crescent filler, con il vantaggio di sporgere meno dal fianco della penna, resta comunque non troppo gradevole sul piano estetico.
sleeve filler
Lo sleeve filler, chiamato anche thumb filler è uno dei tanti sistemi di caricamento sperimentati all'inizio del '900, in particolare venne adottato dalla Holland intorno al 1905 e dalla Waterman che lo utilizzò dal 1910 al 1915. Questo sistema di caricamento si basa sullo spostamento appunto di un manicotto che fascia il fusto della penna per celare una apertura di grandi dimensioni praticata su un lato dello stesso. Spostando il manicotto, che protegge l'apertura, si ottiene un accesso diretto alla barra di pressione (su cui in genere veniva montato un pulsante a rilievo in corrispondenza dell'apertura) che può essere così premuta usando la punta delle dita.
La presenza del manicotto che fascia il fusto in corrispondenza all'apertura rende però non uniformi le dimensioni del corpo della penna, che quindi risultano spesso poco gradevoli dal punto di vista estetico. Inoltre si aumenta di molto la complessità meccanica della penna e la sua fragilità generale, essendo le penne di quel periodo realizzate in ebanite, materiale non particolarmente resistente agli sforzi meccanici. Per questo motivo questo sistema di caricamento ebbe una diffusione ridotta ed venne ben presto abbandonato.
Una seconda versione di questo sistema di caricamento, molto più sofisticata, venne adottata dalla LeBoeuf nel 1930. In questo caso non si aveva un manicotto, ma era l'intero fusto della penna (realizzato stavolta in celluloide) che poteva venire sganciato dal gruppo pennino, andando a scorrere su un cilindro interno realizzato in metallo, sul quale era di nuovo presente una apertura laterale per la pressione diretta sul serbatoio. In questo caso si era ottenuta un fusto uniforme di forma cilindrica che non presentava fessure, neanche per l'alloggiamento della levetta.
In una forma simile, almeno sul piano estetico, questo sistema di caricamento venne adottato anche dalla Parker per l'aerometric usato nella 51 (che però prevede pressioni multiple per la presenza di uno sfiatatoio), mentre un sistema sostanzialmente identico viene utilizzato ancora oggi da alcuni converter (ad esempio quelli delle stilografiche Pilot di fascia bassa).
hump filler
Il sistema di riempimento a sporgenza, quello che nel mondo anglosassone viene denominato hump filler, è in sostanza una variazione sul tema del crescent filler in cui si effettua la compressione del sacchetto utilizzando un elemento sporgente da una apertura laterale della penna. L'elemento consente di comprimere direttamente il serbatoio in gomma, le differenze principali fra le varianti di questo caricamento attengono alle modalità in cui si assicura, in maniera più o meno affidabile, che la sporgenza non possa essere premuta accidentalmente.
Il sistema ebbe una certa diffusione all'inizio del 1900, come alternativa al successo del crescent filler della Conklin, una delle versioni meglio realizzate era il cosiddetto Wawco filler ideato da William Welty (brevetto nº US-834542) ed usato per le penne prodotte da quest'ultimo sia con il marchio Wawco che con gli altri marchi in uso all'azienda.
Caricamenti a leva
Si sono riuniti in questo gruppo tutti i sistemi di caricamento basati sulla compressione meccanica del serbatoio di gomma tramite un meccanismo basato sul principio della leva. Molti di questi sistemi sono nati come tentativo di aggirare il brevetto originale della Sheaffer, o per trovare alternative che potessero distinguere le penne che li utilizzavano rispetto ai concorrenti.
Il principio di questi sistemi di caricamento resta sempre quello della compressione, e successiva espansione per risucchiare l'inchiostro dalla bottiglia, di un serbatoio in gomma; valgono pertanto le considerazioni generali su vantaggi e svantaggi fatte nel paragrafo precedente. La sostanziale differenza è nel meccanismo con cui si effettua la compressione, comunque anche in questo caso si fa in genere ricorso ad una pressure bar rigida, premuta dal meccanismo della leva, per distribuire uniformemente la pressione sul sacchetto.
lever filler
Il caricamento a levetta è probabilmente il sistema di caricamento più diffuso fra le penne d'epoca (ed è anche stato utilizzato, come forma di revival, da alcuni produttori moderni). Introdotto massicciamente sul mercato nel 1912 dalla Sheaffer, che ne ha sempre proclamato l'invenzione, è stato realizzato in innumerevoli varianti e versioni, molte delle quali, spesso tecnicamente inferiori, sono state create soltanto per poter aggirare il brevetto (nº US-896861) che copriva l'invenzione di Walter Sheaffer che origina al 1908.
In realtà la progenitura della Sheaffer è posta seriamente in discussione; esistono infatti versioni precedenti di questo sistema di caricamento, un brevetto dello svedese Johansson del 1898 ed uno dell'americano Barnes (nº US-726495) del 1903, la presenza delle quali ha poi consentito ad altre aziende, come la Waterman, di utilizzare delle varianti dello stesso sistema. E' comunque senz'altro attribuibile ai massicci investimenti della Sheaffer il successo del sistema e la sua enorme diffusione.
Nel caso del brevetto della Sheaffer il meccanismo prevede l'applicazione della pressione al sacchetto utilizzando una leva che va a premere su una barretta metallica elastica (la cosiddetta spring bar) sagomata forma di "J", questa viene inserita nel corpo della penna con la parte curva verso il fondo in modo da fare aderire la parte diritta sul fusto della penna, in corrispondenza della levetta. In molti casi la pressione sul sacchetto non viene esercitata direttamente dalla spring bar, ma a questa viene agganciata ad una pressure bar che è quella che viene premuta contro il sacchetto.
In posizione di riposo la levetta viene alloggiata orizzontalmente in una fessura praticata lateralmente nel corpo della penna. Nella versione originale di Sheaffer essa veniva mantenuta in posizione tramite un sottile perno metallico che la attraversava centralmente, inserito direttamente nel fusto della penna, che veniva traforato per l'occorrenza. Sollevando la levetta da un lato l'altro lato spinge verso il basso la barretta di pressione, che così comprime il sacchetto.
Come accennato esistono numerose versioni diverse di questo meccanismo. La Waterman ad esempio, per eludere il brevetto della Sheaffer, introdusse, basandosi sul brevetto di Barnes, una leva imperniata direttamente all'interno di una gabbietta metallica che conteneva tutto il meccanismo. Questa a sua volta veniva fissata con delle alette alla penna, utilizzando come alloggiamento una apposita fessura laterale creata nel fusto.
Un sistema più efficiente, utilizzato in seguito da altri produttori (compresa la Sheaffer, ma solo dopo la scadenza del brevetto), prevede invece che la levetta sia mantenuta nella sua posizione tramite un anello metallico che la attraversa (brevetto nº US-1292736). Questo viene inserito all'interno della penna e mantenuto in posizione tramite una apposita scanalatura praticata internamente sul fusto, in corrispondenza dell'apertura laterale da cui alloggia la levetta stessa. Questo sistema presenta il notevole vantaggio di una maggiore robustezza meccanica, dato che non necessita di praticare fori per il perno nel materiale del fusto, che nelle penne in ebanite risultava spesso piuttosto fragile.
Altre variazioni del sistema attengono alle modalità con cui la levetta esercita la pressione sul sacchetto: ad esempio la Eversharp non utilizzava una barretta flessibile ma una barretta piatta con i lati ripiegati ad "U", ancorata su un gancio sul fondo della penna. La levetta era dotata sull'estremità esterna di due punte che andavano ad alloggiarsi nel binario ricavato dalla ripiegatura della barretta, in modo da risollevarla in posizione di riposo una volta effettuato il caricamento, inoltre per mantenere bloccata la levetta in posizione di riposo questa era dotata di piccole sporgenze che andavano ad incastrarsi in apposite rientranze create nella fessura di alloggiamento.
La Conklin con la Endura introdusse una versione del caricamento in cui soltanto la metà della levetta che veniva sollevata era esposta esternamente, riducendo le dimensioni della fessura di alloggiamento della stessa. Inoltre il meccanismo utilizzato dalla Conklin, come quello della Eversharp non utilizzava una spring bar, ma una barra di pressione era incastrata direttamente sulla levetta tramite due piccoli gancetti all'interno della stessa, che andavano ad incastrarsi in una apposito aggancio sulla barra.
Una ulteriore variante degna di nota del sistema è quella della Carter, derivata da un brevetto (nº US-1209978) della De Witt-La France, che presenta una sorta di "guinzaglio" attaccato alla levetta che ne impedisce il ribaltamento una volta che questa ha raggiunto la posizione verticale, nell'ottica di evitare danneggiamenti alla penna ed al sistema.
Infine una particolare versione di riempimento a levetta è quello della Skyline della Eversharp, che potrebbe essere classificato anche fra i caricamenti a sfiatatoio. In tal caso infatti all'interno del serbatoio in gomma si ha uno sfiatatoio, e la spring bar è molto corta e volta a comprimere soltanto la parte finale del sacchetto. La penna viene caricata ripetendo più volte l'azione di pressione con la levetta, usando il principio classico dello sfiatatoio. Analogo a questo, anche se realizzato in maniera completamente diversa, è l'Ink-Vue della Waterman.
spoon filler
Il sistema di caricamento denominato spoon filler nel mondo anglosassone (traducibile in "a cucchiaio" da noi) deve il nome alla forma della barra con cui si va ad eseguire la compressione del serbatoio, che ricorda appunto quella di un cucchiaio. In questo caso la pressione viene esercitata sull'estremità allargata del cucchiaio, a cui si accede svitando un fondello di copertura posto sul fondo del corpo della penna. La barra è opportunamente incernierata al fondo del fusto, così che la pressione sul cucchiaio, spostando solidalmente la sezione interna della barra, fa sì che questa vada a premere sul sacchetto.
Hanno usato questo tipo di caricamento varie aziende, come la Columbus, che ne brevettò una versione nel 1929 (nº GB-334913), ma in generale esso introduce una inutile complessità meccanica ed un maggiore stress sui materiali della penna, senza fornire particolari benefici. E' stato adottato per lo più come tentativo di aggiramento dei brevetti sul caricamento a levetta, o come segno di distinzione rispetto agli altri meccanismi, dato che consente di evitare la fessura laterale per la leva, ma non ha mai riscosso un significativo successo.
hatchet filler
In realtà vengono chiamati hatchet filler di due sistemi di caricamento completamente diversi fra loro, a cui però venne dato questo nome dai rispettivi produttori. Il primo è quello usato dalla Holland dal 1908 al 1912; il caricamento prevedeva sempre l'uso di una barra di pressione posta in corrispondenza di una fenditura, soltanto che in questo caso la fenditura era lasciata aperta da una parte, mentre dall'altra veniva disposta una leva a forma di "P".
La leva era incernierata su uno dei suoi estremi (il gambo della "P") in corrispondenza della fine della fenditura, e rientrava con la parte sporgente all'interno del corpo della penna, sul fondo della stessa. Per il caricamento la leva veniva estratta e ribaltata di 180°, per poter andare a premere sulla barra di pressione usando la parte sporgente; una volta portata la leva in posizione di pressione in sostanza il meccanismo diventa analogo al crescent filler, con il vantaggio del non avere sezioni sporgenti (ma con lo svantaggio di una certa fragilità e complessità meccanica).
Il secondo sistema è quello usato dalla Crocker intorno al 1910, in questo caso il fondello stesso è ancorato ad una leva, che alzata in posizione verticale va a comprimere il sacchetto. Per essere utilizzato il fondello veniva svitato, dopo di che si poteva azionare la leva. Tenendolo avvitato la leva veniva bloccata in posizione di riposo, evitando così pressioni accidentali.
Entrambi questi sistemi si possono annoverare fra i vari tentativi di creare un sistema di compressione del sacchetto basato su meccanismi che si distinguessero da quelli brevettati dagli altri produttori. Data la relativa complessità realizzativa e la tutto sommato scarsa efficienza tecnica, entrambi non hanno avuto alcun seguito significativo. La loro rarità li rende però interessanti dal punto di vista collezionistico.
levetta di fondo
Il caricamento a levetta di fondo, detto anche caricamento a leva posteriore, è una particolare versione di caricamento a leva adottato dalla Aurora ed utilizzato a partire all'incirca dal 1930 per il modello Internazionale, ed in seguito usato anche sulla Novum. La prima versione di questo caricamento però è stata utilizzata dalla Curzon per il modello Top Lever (in seguito ridenominato Debrett's) da cui deriva anche il nome adottato in ambito anglosassone per questo caricamento. Dato che il brevetto della Top Lever (nº GB-273357 e nº FR-628272 che è ancora più simile al meccanismo che si trova sulle Aurora) è del 1926, come la Top Lever, non è corretto attribuire l'invenzione di questo caricamento all'Aurora. Non sono note altre varianti del sistema utilizzate da altri produttori tranne lo switch filler della Pilot, che presenta alcune affinità con questo ed ancor di più con la variante adottata in un secondo tempo sulle Superna.
In sostanza il caricamento a levetta di fondo realizza una sorta di incrocio fra il principio della leva ed il meccanismo usato nel caricamento a pulsante di fondo. In questo questo caso la levetta è molto corta e posizionata su una fessura praticata sul fondo della penna, la leva deve essere alzata dalla sua posizione di riposo, in cui è ripiegata dentro il fondello, ed a quel punto spingendola ulteriormente si va ad azionare una barra di pressione interna analoga a quelle usate nel caricamento a pulsante di fondo, che inarcandosi comprime il serbatoio.
Il sistema è piuttosto complesso e delicato (date le piccole dimensioni della leva gli sforzi da applicare sono maggiori), e per evitare di deformare il corpo della penna l'Aurora inseriva un rinforzo all'interno dello stesso (realizzato con un sottile cilindro metallico di alluminio inserito sulla superficie interna) che riduce ulteriormente lo spazio disponibile per il sacchetto.
Il meccanismo consente di evitare la presenza di un fondello di copertura del pulsante di fondo, e dei relativi problemi di smarrimento, al costo di una certa complessità meccanica. La sua principale ragione d'essere, a parte quella di distinguersi dagli altri produttori, resta però quella prevalentemente estetica di evitare una fessura su un lato della penna.
Una variante del sistema, introdotta sempre dall'Aurora con il modello Superna, prevede il montaggio della levetta di fondo in posizione verticale; la levetta viene montata all'interno di una struttura in alluminio inserita sul fondo della penna, che si cura di assorbire gli sforzi. La levetta emerge da una cupola a forma semisferica e può essere azionata tramite una pallina di plastica posta sulla estremità esterna. In questo caso si accede al meccanismo svitando il fondello e si carica la penna spingendo la leva tramite la pallina.
Caricamenti a compressione meccanica del serbatoio
Si sono riuniti in questa sezione tutti gli altri sistemi di caricamento basati sempre sulla compressione meccanica di un serbatoio in gomma, ma effettuata tramite un sistema meccanico che non si riferisca direttamente al principio della leva, e pertanto usati come alternativa legalmente inoppugnabile sul piano brevettuale al sistema introdotto dalla Sheaffer.
button filler
Il cosiddetto sistema a pulsante di fondo (più semplicemente button filler per gli anglosassoni) venne introdotto dalla Parker nel 1913.[2] Il sistema nasce dalla necessità di trovare una alternativa al caricamento a levetta della Sheaffer che non ne copiasse il progetto evitando così tutti i possibili problemi legali dovuti ai brevetti.
In questo caso il sistema prevede che la compressione del sacchetto di gomma sia effettuata attraverso una striscia di metallo flessibile (spesso chiamata "I-bar") che viene fatta incurvare premendola tramite un pulsante posto sul fondo della penna. La striscia in posizione di riposo è diritta ed appoggiata su un fianco del corpo penna. Sul lato inferiore essa viene posta a contrasto con il gruppo pennino (in certi casi viene creata una apposita rientranza sul corpo stesso). Sul lato superiore essa fuoriesce, tramite una estremità incurvata, da un foro praticato sul fondo della penna, ed inserita all'interno di un pulsante metallico.
La pressione del pulsante fa sì che la barretta si fletta incurvandosi verso il centro della penna causando la compressione del serbatoio. Anche in questo caso viene usata una barra di pressione per rendere più uniforme la compressione del sacchetto. Il sistema presenta il vantaggio di non necessitare di una fessura laterale sul corpo della penna. Il fatto poi che l'accesso al pulsante venisse protetto tramite un fondello svitabile consentiva di affermare una maggior sicurezza rispetto alle perdite di inchiostro in caso di rottura del sacchetto, inoltre il sistema veniva promosso per la sua capacità di consentire il caricamento della penna anche con una mano sola.
In realtà oltre ai precedenti vantaggi, questo sistema presenta anche qualche svantaggio. Anzitutto il sistema è più macchinoso e richiede un buon posizionamento della striscia flessibile, inoltre la capacità di riempimento è limitata, non potendo avere il pulsante una grande escursione, ed ottenendo pertanto una flessione, e conseguente compressione, limitata. Infine la pressione del pulsante richiede comunque un discreto sforzo.
Ciò nonostante il sistema ebbe un discreto successo e venne riutilizzato da vari produttori europei. In particolare una variante interessante è il push-knob realizzato dalla Montblanc, in cui il fondello stesso serve da pulsante. Esso infatti può essere svitato parzialmente fino a portarlo in una posizione in cui viene agganciato il pulsante interno su cui è ancorata la molla metallica, premendo il fondello si effettua la compressione della molla ed il relativo caricamento della penna. Una volta completato il caricamento il fondello può essere riportato in posizione di blocco per evitare pressioni accidentali.
Un'altra variante è quella brevettata dalla Soennecken nel 1930, che prevede un pulsante di ebanite nascosto da un guscio ruotando il quale si può raggiungere il pulsante di caricamento ed azionarlo, mentre ruotandolo in direzione inversa questo viene riportato nella posizione originale, bloccando l'accesso al pulsante. Entrambe le varianti consentono di ovviare ad un altro non trascurabile problema della versione classica, che è la non trascurabile probabilità di perdere il fondellino svitabile.
twist filler
Come indicato dal nome, il twist filler o sistema di caricamento a torsione è basato sulla compressione del serbatoio attraverso l'esercizio di una torsione sullo stesso. In questo tipo di caricamento in generale il serbatoio viene realizzato non con un sacchetto, ma con un tubo di gomma la cui estremità posteriore è incollata al fondello del corpo della penna che può essere ruotato, in modo da generare la torsione che strizza letteralmente lo stesso.
Benché presenti alcuni vantaggi rispetto al tradizionale caricamento a levetta, come una maggiore semplicità meccanica ed il pregio dal punto di vista estetico di non necessitare di una apertura laterale sul corpo della penna, il principale difetto di questo sistema, che ne decretò il sostanziale insuccesso, era la maggiore facilità con cui il serbatoio in gomma poteva rompersi a causa del notevole sforzo imposto sullo stesso dalla torsione.
Il sistema è stato usato principalmente dalla A. A. Waterman che intorno al 1902 acquisì un brevetto (nº US-744642 attribuito a Harry W. Stone) ad esso relativo. Altre aziende introdussero sistemi analoghi, o ispirati allo stesso principio della rotazione del fondo della penna per strizzare il serbatoio, come il leverless della Swan. Una versione molto particolare di questo tipo di caricamento è stata impiegata su un prototipo di penna della Nettuno mai commercializzata.
leverless filler
Il sistema di caricamento denominato leverless venne adottato dalla Swan nel 1932 per i modelli omonimi, ed il suo utilizzo era dettato principalmente da motivi estetici. Si tratta in sostanza di una variante del caricamento a torsione in cui però il serbatoio è realizzato con un sacchetto di gomma come nel caricamento a levetta ordinario e la torsione comprensione avviene attraverso una barretta eccentrica ancorata al fondello della penna che in posizione di riposo resta laterale, la cui rotazione comporta una torsione applicata lateralmente al sacchetto con il relativo strizzamento.
Rispetto al caricamento a torsione la sostanziale innovazione introdotta dalla Swan fu quella di consentire una soltanto una rotazione limitata del fondello, marcato con delle frecce, e permette di evitare uno sforzo eccessivo applicato alla gomma del sacchetto. Il caricamento comunque ebbe un successo limitato ed è stato utilizzato soltanto da questa azienda, avendo in sostanza gli stessi problemi di fragilità del suo analogo ed una capacità di carica abbastanza ridotta.
switch filler
Viene chiamata in questo modo, dalla forma del pomello che attiva il riempimento, il caricamento adottato dalla Pilot per la sua linea Super. Si tratta, come si può evincere dal relativo brevetto (nº US-2871825) di un sistema basato sullo stesso principio del pulsante di fondo, in cui si effettua una flessione di una I-bar con l'azionamento di una sorta di interruttore posto sul fondo della penna. Il sistema assomiglia molto al caricamento a levetta di fondo della Aurora, in particolar modo alla variante dotata di pallina utilizzata sulle Superna; a differenza di questo però l'azionamento viene effettuato rimuovendo il fusto della penna per accedere al meccanismo interno.
Caricamenti pneumatici
Si sono classificati in questa sezione i sistemi di caricamento basati sulla compressione pneumatica di un sacchetto di gomma flessibile. Quest'ultimo viene cioè compresso dalla pressione atmosferica generata dal sistema di caricamento per farne uscire l'aria che verrà sostituita dall'inchiostro nella fase di decompressione in cui il sacchetto si riporta, per elasticità, alle sue dimensioni normali.
blow filler
La prima versione funzionante di caricamento pneumatico si può considerare il blow filler creato da Seth Sear Crocker nel 1901 (nº US-678547). Il sistema era molto semplice sia in termini di modalità di funzionamento che di realizzazione costruttiva, ma era veramente molto scomodo da usare.
Nel blow filler infatti la pressione pneumatica viene generata direttamente dall'utilizzatore della penna che deve soffiare (da questo il deriva il nome) all'interno del fusto attraverso un apposito foro praticato sul fondo dello stesso. La pressione così generata comprime il sacchetto interno e permette il conseguente caricamento della penna.
Ovviamente per poter utilizzare il blow filler occorrono buoni polmoni per poter soffiare con forza, ed occorre farlo in una posizione in cui la penna ha il pennino immerso nell'inchiostro, cosa che rende questo sistema di caricamento tutt'altro che comodo. Per questo motivo le penne venivano fornite anche con una pompetta da utilizzare come ausilio per il caricamento.
Per la sua scarsa praticità il sistema ebbe vita breve e venne usato esclusivamente dalla Crocker, che cercò comunque delle alternative con il suo hatchet filler, ma da esso deriva il sistema pneumatico della Chilton realizzato dal figlio di Seth Crocker, che pur essendo uno dei sistemi più originali ed efficaci mai realizzati, non conobbe ugualmente il successo che avrebbe meritato.
pneumatic filler
Nel 1924 Seth Chilton Crocker riprese l'idea del blow filler ideato dal padre Seth Sears Crocker perfezionandolo ulteriormente utilizzando un nuovo brevetto (nº US-1528379, di David J. La France). Il nuovo sistema si basava sul fatto di rendere il corpo della penna scorrevole intorno ad un tubo metallico avvitato sul gruppo pennino cui era montato il classico sacchetto di gomma da comprimere. Per eseguire questa azione il fusto esterno della penna poteva scorrere sul fusto interno e la tenuta stagna fra i due era realizzata da un filo incerato posto in coda al cilindro metallico interno.
Il fusto esterno della penna aveva, come per il blow filler un foro di areazione sul fondo. Il riempimento si otteneva facendo scorrere indietro il corpo della per poi riportarlo in posizione tenendo chiuso con un dito il foro sul fondo. In questo modo la pressione generata sul sacchetto ne provoca la compressione, ma una volta lasciato libero il foro di areazione la successiva espansione del sacchetto causa la suzione dell'inchiostro.
Il sistema era semplice, funzionale e robusto, tutto lo spazio compreso nel fusto interno era utilizzabile per il sacchetto (senza necessità di una barra di pressione come per il caricamento a levetta) che permetteva alla Chilton di avere una autonomia nettamente superiore alle concorrenti. Inoltre questo semplice meccanismo era molto semplice da riparare, bastava svitare il fusto interno per sostituire il sacchetto. Infine la presenza del foro di areazione permetteva di mantenere bilanciata la pressione interna della penna, così che essa non presentava problemi di perdite o di assenza di inchiostro in caso di variazioni di pressione o temperatura.
La semplicità era un punto di forza della Chilton, il fusto esterno non era neanche ancorato al gruppo pennino, dato che questo non era necessario poiché per la precisione meccanica della lavorazione non scorreva durante l'uso. L'unico svantaggio era che per funzionare la penna richiedeva una maggiore lunghezza del gruppo pennino per poter maneggiare la penna una volta ritratto il corpo per il caricamento, che doveva essere effettuato con due mani. Dato che la filettatura per il cappuccio era posta sul fusto esterno della penna, (in modo che questo fosse bloccato quando la penna veniva chiusa), la cosa comportava anche una maggiore lunghezza del cappuccio, e quindi un aspetto poco proporzionato.
Per questo motivo nel 1927 venne creata una seconda versione del sistema di caricamento, in cui il fusto esterno era ancorato in maniera convenzionale al gruppo pennino, ed al suo posto veniva utilizzato per generare la depressione un secondo tubo metallico posto fra questo ed il fusto interno. Il sistema di depressione era ancorato al fondello della penna che costituiva un cappuccio cieco, in questo modo era sufficiente svitare il fondello della penna per effettuare il caricamento, che a questo punto poteva essere eseguito anche con una sola mano.
La Chilton però non sembra essere l'unico produttore ad aver utilizzato questo sistema, infatti un sistema sostanzialmente identico denominato Compressor era stato inventato dalla Montblanc nel 1923 (brevetto nº DE-400356) ed utilizzato dal 1924 al 1929 per alcuni modelli, che però vennero commercializzati su scala ridotta (principalmente in Francia) e non riscossero un successo significativo.
Touch Down
Il sistema di caricamento denominato dall'azienda stessa Touch Down venne introdotto dalla Sheaffer nel 1949 per i modelli omonimi, ed altro non è che una rielaborazione più sofisticata, effettuata dopo venticinque anni (brevetto nº US-2610612), del sistema di caricamento pneumatico della Chilton (il cui brevetto, nº US-1528379, viene citato esplicitamente). Il principio di funzionamento infatti è sostanzialmente identico, quello che cambia è la modalità con cui viene effettuata la compressione pneumatica del sacchetto di gomma interno alla penna.
Anche in questo caso si ha un fondello svitabile che è agganciato ad un cilindro metallico che scorre ermeticamente grazie ad una guarnizione lungo il corpo della penna, il meccanismo è però molto più complesso per evitare l'uso del foro di areazione sul fondo della penna e consentire la compressione soltanto spingendo verso il basso il tubo ancorato al fondello una volta che lo si è estratto.
In questo caso la compressione avviene facendo passare l'aria nell'intercapedine attraverso non un foro sulla punta del cappuccio ma delle brevi scanalatura laterali alla due estremità del tubo interno. In fase di apertura le scanalature sul fondo consentono l'espansione del sacchetto, chiudendo il pistone lo scorrimento è a tenuta e l'aria interna comprime il sacchetto, a fondo corso le altre scanalature permettono all'aria di fuoriuscire e l'espansione del sacchetto carica l'inchiostro.
snorkel
Il sistema di caricamento a cui spesso si fa semplicemente rifermento come snorkel (anche se questo è solo uno dei componenti) venne introdotto dalla Sheaffer nel 1952 con la Snorkel Pen. Il sistema rappresenta una evoluzione del precedente Touch Down, il meccanismo di caricamento infatti è esattamente lo stesso, ed utilizza una compressione pneumatica realizzata allo stesso modo.
La novità infatti attiene non tanto alla modalità in cui viene aspirato l'inchiostro quanto al fatto che in questo caso non è più necessario caricare la penna immergendo il pennino all'interno della boccetta. In fase di apertura infatti si puo far estendere attraverso l'alimentatore un tubicino metallico (lo snorkel, appunto). con un condotto di areazione che consente fare effettuare il passaggio dell'inchiostro attraverso di esso anziché dal pennino.
Si tratta senza dubbio di uno dei più complessi (e per certi versi affascinanti) sistemi di caricamento mai utilizzati, che permette di non sporcare il pennino e che per questo veniva ampiamente pubblicizzato. Il principale svantaggio resta quello della capienza, in genere infatti l'unità di caricamento che contiene il sacchetto è abbastanza piccola e la penna contiene poco inchiostro.
Caricamenti a sfiatatoio
Questi sistemi di caricamento sono accomunati dallo sfruttare la presenza di un tubetto con funzioni di sfiatatoio (il cosiddetto breather tube) che consente di eseguire il caricamento ripetendo più volte una qualche azione meccanica (diversa a seconda dei diversi sistemi di caricamento) che consente di creare una compressione dell'aria all'interno del serbatoio della penna. Le varietà di maniere in cui questa compressione viene effettuata è risultata estremamente ampia, ma nella maggior parte dei casi prevede un qualche meccanismo che agisce su un bulbo flessibile, anche se esistono meccanismi alternativi, come quello che si trova su alcune Ancora Lusso in cui la depressione si fa con uno stantuffo di corsa molto breve.
Lo sfiatatoio è inserito nell'alimentatore e mantenuto in posizione centrale rispetto al corpo della penna che normalmente viene a svolgere la funzione di serbatoio. In fase di compressione l'aria presente esce dallo sfiatatoio, da cui, a causa della depressione venutasi a creare, viene caricato l'inchiostro che finisce nel serbatoio; la presenza dello sfiatatoio fa sì che l'inchiostro caricato non venga espulso nelle successive fasi di compressione, fintanto che non si arrivi a riempire tutto il serbatoio fino al livello dello sfiatatoio.
La presenza dello sfiatatoio in alcune realizzazioni ha inoltre un secondo effetto positivo perché consente di equilibrare immediatamente la pressione dell'aria interna al corpo della penna con quella dell'aria esterna, dato che in questo caso lo sfiatatoio fornisce una via di comunicazione fra interno ed esterno, si evitano così i vari problemi di fuoriuscita dell'inchiostro in caso di sbalzi di pressione.
bulb filler
Il caricamento a pompetta o bulb filler è probabilmente il capostipite dei sistemi di tutti i sistemi caricamento basati sulla presenza di uno sfiatatoio. Le sue origini sono incerte, uno dei brevetti più vecchi (nº US-802668 del 1905) era assegnato alla Aikin Lambert, ma ne esiste uno ancora precedente (nº US-723726 del 1903 che non pare essere stato utilizzato). Ma al di la dei precursori uno dei primi modelli ad essere stato prodotto massicciamente ed immesso sul mercato è senz'altro quello della Postal del 1925, anche se la versione più sofisticata resta probabilmente quella della Stylomine 303. In seguito lo stesso sistema è stato anche adottato dalla Eversharp per il modello Bantam e per la versione da stenografe-centraliniste dalla Doric, e dalla Pelikan per la Rappen.
Il sistema prevede l'uso diretto del corpo della penna come serbatoio, consentendo anche, quando questo viene realizzato in materiale trasparente, la visualizzazione del livello d'inchiostro. Il caricamento viene effettuato tramite la pressione su una pompetta di gomma, analoga a quella di un contagocce, inserita direttamente sul fondo del corpo della penna, ed a cui si accede svitando il fondello della stessa. Data la necessità di avere una pompetta di dimensioni sufficienti, questo in genere comporta su questo tipo di penne un fondello molto più lungo rispetto a quello usato su altri caricamenti, come quello a pulsante di fondo o a stantuffo.
Il principio di caricamento deriva da quello del contagocce, si immerge la punta della penna nell'inchiostro e si preme la pompetta, la relativa espansione causa una depressione che fa affluire l'inchiostro dentro il corpo della penna. L'innovazione creata da questo sistema di caricamento è costituita proprio dalla presenza dello sfiatatoio collegato al gruppo pennino e direttamente connesso con un condotto al foro di ventilazione del pennino.
Questo fa sì che si possa ripetere la pressione sulla pompetta più volte, per effettuare diverse azioni di caricamento e riempire progressivamente la penna. In assenza dello sfiatatoio infatti, con la compressione della pompetta si farebbe fuoriuscire l'inchiostro presente nel corpo non essendovi sfogo per l'aria contenuta nello stesso, ottenendo così una capacità molto limitata; lo sfiatatoio fornisce invece una via d'uscita all'aria presente nel serbatoio che viene compressa dalla pompetta, ed una via di ingresso per l'inchiostro che viene risucchiato dalla depressione. Si può così ripetere la compressione della pompetta e continuare a caricare inchiostro fintanto che quest'ultimo non supera il livello dello sfiatatoio, riempiendo totalmente la penna.
vacumatic
Introdotto dalla Parker nel 1933 con il lancio sul mercato della omonima Vacumatic, venne pubblicizzato come il primo sistema di caricamento senza sacchetto di gomma (sacless). In realtà questo non è assolutamente vero (un classico esempio di pubblicità ingannevole) sia perché all'epoca esistevano già parecchie versioni di sistemi di caricamento senza sacchetto di gomma, come la siringa rovesciata della Onoto ed il caricamento a stantuffo della Pelikan, sia perché in realtà il caricamento si affida sempre ad un elemento di gomma flessibile, il diaframma (o diaphragm, come si indica nel mondo anglosassone), anche se questo non svolge le funzioni di serbatoio.
Fra i vari sistemi di caricamenti basati sull'uso di uno sfiatatoio il Vacumatic è senz'altro uno dei più complessi, ma in realtà non è che una rielaborazione del meccanismo del precedente bulb filler in cui invece di usare una pompetta la compressione dell'aria nel corpo della penna viene fatta attraverso il movimento di una membrana di gomma, il diaframma appunto. In questo caso il movimento viene effettuato attraverso la pressione su un pulsante a molla posto sul fondello della penna, che agisce sul meccanismo che sposta la membrana. Ripetendo più volte la pressione si ottiene lo stesso risultato di pompaggio di una normale pompetta di gomma.
Questo meccanismo comporta il vantaggio di poter disporre di un fondello più corto, che rende l'aspetto della penna più gradevole, questo era ancor più evidente nelle prime versioni del sistema, denominate "lockdown", in cui il pulsante, realizzato con un cilindretto di metallo con una scanalatura laterale, poteva essere mantenuto in posizione premuta grazie alla presenza di una terminazione ad "L" della scanalatura stessa, che ne consentiva l'aggancio al meccanismo tramite una rotazione, così poi da consentire la chiusura del fondello stesso (a vite).
Del sistema venne prodotta, a partire dal 1937, una seconda versione denominata "speedline", in cui la realizzazione era semplificata eliminando il sistema di bloccaggio. Questo comportava un fondello più lungo, ma venne pubblicizzato per la possibilità di effettuare il riempimento con una sola mano (in realtà per svitare il fondello se ne usano comunque due). Dal 1942 circa il sistema venne ulteriormente revisionato (con la versione chiamata "wartime" dai collezionisti) usando un pulsante in celluloide anziché in alluminio.
aerometric filler
Introdotto dalla Parker nel 1948, come nuovo sistema di caricamento adottato sulla 51 al posto del precedente vacumatic. In realtà per le modalità di funzionamento questo sistema è molto simile anche allo sleeve filler utilizzato dalla LeBoeuf in quanto si basa sulla pressione di un sacchetto di gomma da effettuarsi da una apertura laterale sul cilindro metallico che contiene lo stesso a cui si accede svitando dalla sezione pennino il corpo della penna.
A differenza del classico sleeve filler il caricamento aerometric prevede però la presenza di uno sfiatatoio all'interno del sistema, cosa che richiedere di ripetere la pressione della barretta quattro o cinque volte (come riportato sulle istruzioni incise su alcune di esse) per poter completare il caricamento. Si può pertanto interpretarlo come una fusione fra uno sleeve filler ed il precedente vacumatic.
In realtà il nome aerometric viene usato in questo senso per lo più dai collezionisti, l'azienda faceva piuttosto riferimento con il nome di Aero-metric Ink System (riportato ad esempio in pubblicità come questa) all'insieme del sistema di caricamento (chiamato Foto-fill filler), dell'alimentatore e del nuovo serbatoio in PVC (chiamato Pli-glass), cosa che consentiva all'azienda di proclamare la penna come non contenente nessuna parte in gomma.
stantuffo tuffante
Lo stantuffo tuffante è nome dato al sistema di caricamento inventato e brevettato dalla OMAS nel 1936 con l'introduzione del modello Lucens. In realtà un sistema di caricamento sostanzialmente identico a questo ed altrettanto funzionale si trova sulle penne realizzate della Dunn risalenti a ben quindici anni prima. Per questo motivo, pur non potendo stabilire o meno l'originalità dell'invenzione della OMAS non è comunque corretto assegnare ad essa la paternità completa di questo tipo caricamento, anche se oggi in Italia si fa riferimento a esso con il nome di stantuffo tuffante per la maggiore notorietà raggiunta dalla Lucens rispetto alle penne della Dunn e per il fatto che questa non avesse dato un nome specifico al suo caricamento.
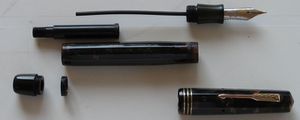
Il principio di funzionamento resta quello di tutti i sistemi di caricamento a sfiatatoio, solo che in questo caso la pressione interna al corpo della penna viene esercitata attraverso un pistone cavo cui si accede dal fondello, che presente una parte finale allargata, ma forata al centro in modo da poter scorrere abbondantemente intorno allo sfiatatoio, che in questo caso è molto lungo ed arriva vicino alla fine della penna.
Svitando il fondello è possibile estrarre il pistone cilindrico, che scorre a tenuta rispetto al corpo della penna ed effettuare tramite esso l'azione di pompaggio. Il meccanismo è molto funzionale e nettamente più evoluto del vacumatic e degli altri sistemi analoghi perché a differenza di questo non necessita di membrane o altri elementi flessibili in gomma, e presenta una maggiore semplicità meccanica. Lo svantaggio è costituito da un ingombro leggermente maggiore del meccanismo.
Nonostante sia fra i più evoluti, efficaci ed interessanti fra i sistemi di caricamento, che presenta tutti i pregi degli altri sistemi a sfiatatoio e nessuno dei problemi legati alla presenza di membrane flessibili in gomma, lo stantuffo tuffante ha purtroppo avuto una scarsa diffusione, che lo vede limitato nel suo utilizzo alle penne della Dunn ed al citato modello Lucens della OMAS.
Ink-Vue filler
Viene chiamato Ink-Vue filler (o caricamento Ink-Vue) una delle tante varianti di caricamento a sfiatatoio nate dopo l'ingresso sul mercato della Vacumatic della Parker. In questo caso si tratta del sistema di caricamento adottato dalla Waterman per il suo modello Ink-Vue, da cui origina il nome, anche se in realtà lo stesso caricamento si trova anche in alcune versioni della Lady Patricia.
In questo caso il principio resta lo stesso, il corpo è realizzato in materiale trasparente che lascia intravedere il livello dell'inchiostro, da cui appunto deriva il nome Ink-Vue, ed il caricamento è effettuato attraverso la compressione di un gommino, solo che a differenza dell'ordinario bulb filler in questo caso la compressione viene eseguita attraverso un meccanismo a levetta montato sulla parte finale della penna.
Il sistema prevede che si apra la levetta e si effettuino una serie di compressioni per pompare l'inchiostro. Ne esistono due versioni, uno con levetta intera (brevetto nº US-2068419), ed uno con levetta snodabile (brevetto nº US-2087672). Inoltre una versione successiva (brevetto nº US-2217755), adottata sul modello denominato 5116, consentiva di costruire la penna con un corpo realizzato in un pezzo unico e non in due parti assemblate l'una sull'altra come per i modelli precedenti.
Il sistema, ancorché funzionante, risulta piuttosto macchinoso con una discreta complessità meccanica, cosa che lo rende abbastanza delicato e piuttosto difficile da riparare. Non riscosse un gran successo, sia per questi motivi che per il difetto estetico di necessitare di una levetta esterna che rompeva l'uniformità del corpo della penna.
Visofil filler
Questo caricamento, creato dalla Swan, prende il nome dall'omonimo modello Visofil sul quale venne impiegato. Si tratta in sostanza di un'altra delle innumerevoli variazioni sul tema del caricamento a sfiatatoio realizzate dopo il successo della Vacumatic della Parker. Di questo sistema esistono sostanzialmente due versioni, la prima, più antica, derivata dal brevetto nº GB-451275 del 1934, ed una evoluzione, derivata dal brevetto nº GB-480965 del 1936.
...da finire...
... in cui questo viene effettuato attraverso la compressione di un cilindro di gomma posto fra il gruppo pennino ed uno stantuffo di plastica trasparente (di forma ottagonale) cui si ...
accordion filler
Viene chiamato così in ambito anglosassone l'originalissimo e funzionale sistema di caricamento a fisarmonica adottato dalla Stylomine per la sua 303 brevettato nel 1938 (nº FR-854177) che alla scadenza del brevetto venne poi adottato anche da molti altri produttori francesi. Il sistema è basato sull'uso di uno speciale sacchetto di gomma elastico con i bordi ondulati, che può essere premuto ed espanso (attraverso un pulsante nel fondello) come si fa appunto con una fisarmonica.
All'interno del sacchetto è presente uno sfiatatoio che consente, con il solito principio utilizzato da tutta la classe di questo tipo di sistemi di caricamento, di caricare progressivamente la penna pompando l'inchiostro all'interno del sacchetto. Il sistema risultava efficiente e funzionale, e anche più robusto, relativamente allo stress imposto alla gomma del sacchetto, rispetto a buona parte delle alternative. ... (da finire)
Caricamenti a depressione
Si sono riuniti in questo gruppo tutti quei sistemi che prevedono che il caricamento avvenga attraverso la realizzazione di una depressione all'interno del corpo della penna in modo che l'inchiostro venga risucchiato tramite questa. In questo caso è in genere il corpo stesso della penna a fare da serbatoio, e può essere costruito in materiale trasparente così da consentire la visualizzazione del livello di inchiostro.
Come per gli altri sistemi che usano il corpo della penna come serbatoio anche in questo caso si ha il vantaggio di poter disporre di un maggior volume per contenere l'inchiostro, ma si ripresenta lo svantaggio che l'aria residua contenuta nel serbatoio è sensibile alle variazioni di temperatura, il che rende più facile, per l'aumento di volume in caso di riscaldamento, i casi di perdite di inchiostro, specie quando la penna è quasi scarica ed il volume di aria maggiore.
pump filler
In genere si fa riferimento con il nome pump filler al particolarissimo sistema di caricamento adottato dalla Waterman su alcuni modelli dal 1903 al 1910,[3] e basato su un brevetto (nº US-646383, chiesto nel 1897) di William I. Ferris, il progettista che ha prodotto moltissime delle innovazioni degli anni d'oro dell'azienda.
Si tratta di un sistema di caricamento veramente interessante, basato sull'uso di un fondello svitabile, che normalmente è chiuso e mantiene la tenuta della penna, che consente di operare su un pistone sottostante collegato con un alberino snodabile, quest'ultimo ha un foro tenuto chiuso in fase ascendente da una pallina. Immergendo la penna nell'inchiostro quando di spinge in basso il pistone l'aria esce dal foro spostando la pallina, mentre tirando la pallina chiude il foro e consente di aspirare inchiostro.
Benché tecnicamente molto interessante, il sistema non ebbe molta fortuna, anche per la delicatezza del sistema e la necessità di una tenuta non facile da ottenere con i materiali dell'epoca, le penne che lo usano sono pertanto assai rare e molto ricercate dai collezionisti.
syringe filler
Sistemi di caricamento |
Il caricamento a siringa (syringe filler per gli angolosassoni) utilizza il più classico metodo di creare una depressione, quello di spostare uno stantuffo all'indietro in un corpo cavo cilindrico, esattamente come si fa per le siringhe. Il sistema è di semplicissima realizzazione meccanica, ed è stato usato in molte versioni di penne di fascia bassa proprio per la sua economicità. Il sistema viene in genere realizzato con un alberino di metallo o plastica inserito tramite un foro nel fondo della penna a cui si accede rimuovendo un fondello (di norma a vite). Sull'altro estremo dell'albero, quello inserito nel corpo della penna, è montata una guarnizione a tenuta.
Il caricamento avviene spingendo fino in fondo l'albero una volta accedutovi dal retro della penna, e poi risucchiando l'inchiostro, esattamente come si fa con una siringa, tirandolo indietro. Il grosso svantaggio di questo sistema di riempimento è dovuto al fatto che esso richiede di ospitare nel corpo della penna l'albero della siringa, che in posizione di utilizzo è completamente estratto ed in posizione sporgente; questo significa che circa metà dello spazio utile viene occupato da esso e non può essere utilizzato.
Per questo motivo sono state ideate ingegnose varianti del meccanismo basate sui più vari accorgimenti che consentissero di accorciare l'albero della siringa una volta eseguito il caricamento, come il realizzarlo in forma telescopica, o ripegabile, o smontabile. Tutti meccanismi che consentivano una maggiore escursione a parità di lunghezza, al costo però del principale vantaggio del sistema, quello dell'economicità e della semplicità meccanica.
plunger filler
Il caricamento a siringa rovesciata, chiamato usualmente plunger filler dai collezionisti anglosassoni, è, quando ben funzionante, uno dei più semplici ed efficaci sistemi di riempimento, ed è probabilmente anche quello che consente di caricare la maggior quantità di inchiostro a parità di volume della penna. Inoltre è anche uno dei più antichi, essendo stato introdotto per la prima volta sul mercato nel 1905, con il lancio della Onoto.
La creazione di questo caricamento, almeno nella prima versione utilizzabile, si può attribuire a George Sweeter, che ne cedette il brevetto a Evelyn De La Rue per la realizzazione della Onoto. Molto più tardi, in risposta alla moda delle penne trasparenti che consentissero di visualizzare il livello di inchiostro, esso venne adottato anche della Sheaffer a partire dal 1934 con il nome di Vacuum-Fil[4] e dalla Eversharp nel 1937. Nelle penne giapponesi un meccanismo molto simile veniva usato solo come sistema di sicurezza per penne con riempimento a contagocce.
Il principio di funzionamento, come espresso dal nome, si basa sull'inversione del meccanismo della siringa (anche se forse l'analogia sarebbe maggiore con la pompa di una bicicletta), in cui si usa il pistone della siringa, invece che per risucchiare l'inchiostro, per espellere l'aria dal corpo della penna e creare una depressione che poi è quella che consente di effettuarne il riempimento.
Dal punto di vista meccanico il sistema è simile al precedente caricamento a siringa, l'aria viene espulsa spingendo tramite il fondello della penna un pistone costituito da un alberino sulla cui testa è montata una guarnizione in gomma che scorre a tenuta rispetto al corpo cavo della penna, esattamente come il pistone di una siringa. L'alberino fuoriesce, tramite una guarnizione a tenuta, dal fondo della penna per agganciarsi al fondello della stessa che viene utilizzato come maniglia per operare il caricamento. La parte finale del corpo della penna, in corrispondenza alla posizione di riposo del pistone, presenta però un allargamento, così che esso non sia più a tenuta.
Ciò rende possibile, a differenza della siringa classica, effettuare il caricamento reinserendo il pistone all'interno del corpo della penna: con l'espulsione dell'aria così ottenuta si crea una depressione dietro la testa del pistone, che quando questo raggiunge la posizione finale della sua corsa, in cui non vi è più tenuta rispetto al corpo della penna, causa il risucchio dell'inchiostro all'interno della stessa.
Il meccanismo presenta molti vantaggi in quanto lo spazio da esso occupato è molto ridotto, per cui, fintanto che le guarnizioni sono a posto, si ottiene una enorme capacità di caricamento. Il suo problema principale è però proprio quello della perfetta tenuta delle guarnizioni, queste infatti devono sopportare una depressione piuttosto forte, e capita piuttosto spesso che esse, pur garantendo dalle perdite, non consentano un caricamento efficace.
Inoltre una buona tenuta, essenziale per il funzionamento, comporta anche la presenza, a penna scarica, di un grosso volume di aria ben isolato presente all'interno del corpo della stessa, cosa che rende le penne dotate di questo sistema di caricamento molto sensibili alle variazioni di pressione (con il rischio di conseguenti fuoriuscite di inchiostro).
Inoltre, soprattutto con i modelli americani della Sheaffer e dalla Eversharp, la guarnizione sul fondo, che è essenziale per il funzionamento del sistema, tende a deteriorarsi abbastanza rapidamente. Per le due aziende citate la sua sostituzione però comporta la completa sostituzione del fondo stesso della penna, che doveva avvenire con dei ricambi che oggi non esistono più. Pertanto le penne con caricamento a siringa rovesciata hanno una fama di essere difficili da riparare e di funzionamento incerto, anche se in realtà tutto ciò non si applica affatto alle Onoto, che sono piuttosto semplici da riparare e ben funzionanti anche dopo diversi decenni.
piston filler
Sistemi di caricamento |
Il caricamento a stantuffo (chiamato usualmente piston filler nel mondo anglosassone) venne ideato da Theodor Kovacs, un ingegnere ungherese che aveva prestato servizio come ufficiale dell'esercito durante la prima guerra mondiale, che lo brevettò nel 1923, anche se la prima stilografica ad utilizzarlo comparve solo nel 1929, con il lancio della Pelikan 100 che segnò l'ingresso della Pelikan nel mercato delle stilografiche.
Il meccanismo originale, di cui sono state comunque realizzate numerose varianti, prevede la presenza di una doppia vite elicoidale azionata da un fondello. La rotazione di quest'ultimo consente di far scendere e salire il pistone dello stantuffo all'interno del corpo della penna, che assume la funzione di serbatoio. Da allora sono state elaborate innumerevoli varianti del meccanismo che consente lo spostamento dello stantuffo.
Dalla sua introduzione il meccanismo venne adottato in breve tempo prima da tutti i produttori tedeschi e poi da buona parte di quelli italiani. A parte la Nozac della Conklin non ebbe invece praticamente alcuna diffusione negli Stati Uniti, ed una scarsa diffusione anche negli altri principali paesi produttori (Giappone e Regno Unito).
Il principale vantaggio del caricamento a stantuffo è la maggiore capienza, a parità di volume, rispetto a qualunque altro meccanismo basato su un sacchetto di gomma, insieme alla possibilità di consentire la visualizzazione dell'inchiostro in caso di corpo trasparente. Inoltre questo tipo di caricamento, ancorché più complesso meccanicamente, si è sempre rivelato molto più resistente all'usura di altri sistemi, sia per l'assenza di parti in gomma che tendono a indurirsi, che di parti in metallo flessibile che tendono ad arrugginire o rompersi.
Esso risulta però nettamente inferiore in termini di capacità, per il volume necessario ad ospitare il meccanismo, rispetto ad altri caricamenti come quello a siringa rovesciata. Il sistema infatti prevede che la parte superiore del corpo penna sia occupata dal meccanismo, e la parte utilizzabile come serbatoio (quella coperta dall'escursione del pistone) resta solo una frazione del corpo della penna. Alcune varianti, come lo stantuffo telescopico introdotto dalla Luxor e adottato poi anche dalla Montblanc nel 1935, consentono però di diminuire nettamente la lunghezza del meccanismo, ottenendo una capacità superiore, al prezzo di una notevole complessità meccanica (e relativa fragilità).
Altri
Si sono riuniti in quest'ultimo gruppo tutti gli altri sistemi di caricamento, accomunati proprio dal fatto di non aver un fattore comune che consente di classificarli in maniera omogenea.
capillarity filler
Il primo esempio di stilografica con caricamento a capillarità (capillarity filler per gli anglosassoni) è stato il modello 61 lanciato dalla Parker nel 1956. Questo sistema di caricamento (un primo brevetto è il nº US-2462929) è probabilmente uno dei più originali fra quelli che sono stati creati nel corso della storia della produzione di penne stilografiche, e costituisce forse anche l'ultimo tentativo di realizzare un sistema di riempimento completamente diverso, che non riprendesse in qualche modo gli altri meccanismi adottati nel corso degli anni.
Il sistema prevede infatti che il caricamento avvenga semplicemente svitando il corpo in plastica che protegge il serbatoio ed immergendo la parte finale di questo (corrispondente al fondo della penna) nella boccetta di inchiostro. L'effetto della capillarità farà affluire l'inchiostro all'interno del serbatoio caricando così la penna senza necessità di compiere un qualunque tipo di azione meccanica. La 61 venne così promossa come the pen that fills itself (la penna che si riempie da sola).
Il sistema è realizzato grazie ad un serbatoio dell'inchiostro strutturato come camera capillare in grado di assorbire l'inchiostro poi rilasciato verso il pennino, ma nonostante il fascino di un sistema senza parti meccaniche il suo funzionamento si è sempre dimostrato assai problematico. La capacità del sistema infatti era alquanto ridotta, essendo il serbatoio occupato dal sistema capillare, inoltre questo si è dimostrato assai delicato, e prono all'intasamento dovuto alla essiccazione dell'inchiostro, che una volta avvenuta rendeva la penna sostanzialmente inusabile a meno di un lungo ciclo di pulizia.
Per questo ebbe scarso successo, anche se conta qualche imitatore, gli unici altri modelli noti ad avere adottato questo caricamento sono la economica X-Pen della Waterman ed alcuni modelli (Inkmaster, Inkmaster-De-Luxe e 100 capillary pen) della Platignum. Per la sua scarsa usabilità anche nella Parker 61 venne abbandonato dopo qualche anno, per essere sostituito da un più pratico ed ordinario caricamento a cartuccia/converter.
cartridge filler
In questo caso non si può propriamente parlare di sistema di riempimento, dato che non c'è niente da riempire. Il caricamento a cartuccia (cartridge filler per gli anglosassoni) si basa sull'inserimento all'interno del corpo della penna, su un aggancio predisposto sul gruppo pennino, di una cartuccia di plastica piena di inchiostro, da gettare e sostituire con una nuova una volta che questo sia esaurito. In generale poi ogni produttore tende a realizzare cartuccia ed aggancio in maniera diversa, per cui spesso l'unico modo di utilizzare penne d'epoca che fanno uso di questo sistema di caricamento è quello di procurarsi una cartuccia originale usata e riempirla con una siringa.
Parlare dell'invenzione di questo sistema di caricamento risulta essere ambiguo e problematico, dato che esistono vari esempi di precursori fin dai primi decenni del '900, per non parlare del brevetto della Eagle (nº US-426758) del 1890, basati sull'uso di cartucce in vetro. Un altro precursore importante è la John Hancock che negli anni '20 mise in commercio una penna con cartucce in rame (brevetto nº US-1671125).[5]
Fra i precursori è da ricordare infine quello adottato nel 1936 dalla filiale francese della Waterman, che in seguito riprenderà l'idea per la CF. L'uso delle cartucce in vetro per l'inchiostro però conobbe mai una grande diffusione, dato che queste avevano comunque un costo di produzione significativo, e presentavano tutti gli inconvenienti del materiale, primo dei quali la fragilità.
Per questo si tende più propriamente a far risalire le origini della diffusione del caricamento a cartuccia al 1953, con l'introduzione sul mercato del modello CF, sigla appunto di Cartridge Filler, creato ancora una volta dalla filiale francese della Waterman, che di lì a qualche anno avrebbe assorbito i resti della fallita casa madre. E' in tale occasione infatti che viene introdotto un sistema che fa uso cartucce di inchiostro usa e getta realizzate industrialmente in plastica a stampo. In ogni caso il primato è contestato dalla Duo-Cart che pur essendo entrata sul mercato nel 1954 è basata su un brevetto precedente quello della Waterman.
Data la semplicità costruttiva della penna ed i bassi costi di produzione delle cartucce, il caricamento a cartuccia rappresenta oggi il sistema più diffuso per usare una stilografica. Dal punto di vista della praticità infatti è imbattibile, ed il suo difetto principale, la scarsa capienza, può essere ovviato facilmente portandosi dietro un adeguato numero di cartucce, anche se in questo caso perde parte della sua comodità.
converter
In questo caso non si può parlare propriamente di un sistema di caricamento in quanto esistono diversi tipi di converter, che a loro volta usano i più vari meccanismi. In realtà quando si parla di converter si indica semplicemente un sistema meccanico da inserire su una penna al posto di una cartuccia, che consente di eseguire il caricamento della stessa da una boccetta di inchiostro.
Il meccanismo più utilizzato è quello di un minuscolo sistema a stantuffo, riprodotto nel converter stesso. Un altro meccanismo molto comune è quello con cui si effettua la pressione diretta di un serbatoio in gomma (in sostanza uno sleeve filler). Un converter molto particolare è il CON-70, usato nelle penne Pilot di fascia più alta, che prevede l'uso di un ingegnoso sistema a depressione che consente una notevole capienza di inchiostro, confrontabile con quella di una penna a stantuffo di piccole dimensioni.
Riferimenti esterni
- [1] Pagina degli schizzi originali usati in questa pagina
- [2] Pagina sui sistemi di caricamento dal sito di Richard Binder
- [3] Pagina sui sistemi di caricamento dal sito di David Nishimura
- [4] Pagina sui sistemi di caricamento su Penspotters
- [5] Articolo sui sistemi di caricamento su PenTrace, prima parte
- [6] Articolo sui sistemi di caricamento su PenTrace, seconda parte
- [7] Articolo di Jim Mamoulides sul caricamento a pulsante di fondo della Parker
- [8] Articolo su Penexchange sul caricamento a stantuffo
- [9] Articolo su Penexchange sui caricamenti penumatici
- [10] Articolo su Penexchange sul caricamento a pulsante di fondo
Note
- ↑ l'azienda però lo ha fatto utilizzando molti brevetti di Francis C. Brown, della Caw's, che è stata la prima marca ad utilizzarlo, sia pure in versione più primitiva.
- ↑ almeno secondo quanto riportato su questa storia dei modelli iniziali della Parker, i primi brevetti della Parker relativi al caricamento, nº US-1346045 e nº US-1486246, sono rispettivamente del 1919 e del 1922, sicuramente posteriori all'introduzione, dato che anche la Duofold è del 1922 e il sistema compare anche in pubblicità del 1916, in questa discussione però viene riportato l'acquisto da parte della Parker del brevetto nº US-787152, che è del 1905.
- ↑ la data di dismissione del 1910 è incerta, il sistema viene considerato come sostituito dallo sleeve filler a partire da quell'anno, e la produzione non è confermata, ma viene pubblicizzato almeno fino al settembre del 1921 (come verificabile qui).
- ↑ ma solo sui modelli economici, sia per la linea Wasp che per quella chiamata con questo nome, verrà utilizzato sui modelli dell'azienda marcati Sheaffer (le Balance) solo a partire dall'anno successivo, il brevetto originale della ditta, (nº US-1926405), è del 1933.
- ↑ detenuto dalla Pollock Pen Company, che produceva queste penne.
Ringraziamenti
Un grazie di cuore a Fabio Moricci, il Pennaio, che ci ha gentilmente concesso l'uso dei suoi schizzi come base per la realizzazione degli schemi tecnici dei vari sistemi di caricamento.